Red tags are important safety tools that protect workers from dangerous equipment. Sites often use them to identify and sort out damaged tools, which plays a role in the 5S process.
The goal of a 5S program is to create an organized workspace and to ensure that it stays organized. This ongoing process relies on commitment from both workers and managers to oversee workspace cleanliness and correct issues as they arise.
Many sites, however, can take this program to the next level and use red tags to learn more about areas like training, process safety, and more. Once you set up a red tag station and create a log of all red-tagged equipment, you can use the data you gather to deep dive areas of improvement across your site.
Creating a 5S location for red-tagged equipment
Workers are at an increased risk of injury if they use broken or damaged equipment. That’s why you need a designated storage 5S location for all your red-tagged tools.
This area doesn’t have to be fancy—it just needs to be functional. And it needs to be accessible to all departments that would use it. So, if you have a very large facility, you’re probably going to need more than one red tag 5S location.
If the area is for large equipment, make sure that people can get in and out without tripping over items. And if the area is for smaller tools (tape machines, printers, etc.), make sure you add shelving to keep the space organized.
Each storage location should be properly labeled so that it’s easy for people to follow the 5S. Also, don’t forget to include pens and red tags—you don’t want people to improvise with flimsy papers and/or stickers that fall off the equipment. This would make it impossible to catalog and track all the red-tagged items, a practice that can help you improve your operation when done correctly.
Tracking each red tag for 5S adherence
The tagging process is great for removing hazards from the workspace. But there’s still more work to be done once you’ve taken a piece of equipment out of service. You need a system for tracking the tags that come into your designated 5S area.
How you tackle the repair and/or disposal of unsafe equipment largely depends on the tracking systems you already use. Some facilities teams use a ticketing system to log new pieces of equipment into their pipeline. When a technician looks at a red-tagged item, he or she updates the log to include things like:
- The problem with the equipment
- Any tools or materials needed to fix it
- The status of the repair
Another option is to use your site’s action tracking software to log red tag events. The good thing about the software is that you can assign action items to any team or individual.
So, if a member of the EHS team goes through the red tag drop zone and inputs action items, they can assign those tasks to someone on the maintenance team. This cuts out a step of administrative work for the facilities team while also helping the safety team log hazards and document progress towards eliminating them.
While more cumbersome, you can also catalog the red tag 5S area by hand. All you need is a log of the equipment that comes in and out of the 5S area. The data that you’ve collected either digitally or manually can then give you insight into some patterns at your site.
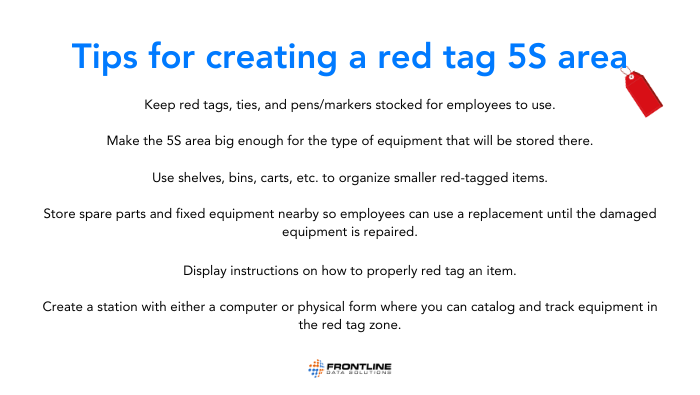
Learning from red tags
Using the log from your red tag 5S area, organize entries according to things like:
- Identification number
- Type of equipment
- Location within the site
- Intended function
- Material
Then, look for commonalities that tell you more about problem areas or pieces of equipment.
For example, does a certain type of equipment (I.e., conveyor belt) account for most repairs?
Or maybe you notice that broken equipment keeps coming from a certain department.
These insights can tell you where to focus your energy on preventing future equipment failures.
You might find a serious usage issue where a department needs to redo training on a specific type of equipment. An example of this is if you were to keep having red-tagged PIT with damaged forks, only to find out that the damage is from user failure.
Or you might learn that the damage is coming from an unsafe PIT lane, parking area, or other 5S-related hazard.
With this information, you can take your red tag procedure to the next level and use historical data to solve a problem. This will lead to lower equipment repair and replacement costs, and it will also increase safety engagement among your workforce.
Other posts you might like…
No posts