The change management process in food industry operations is for coordinating major modifications so they disrupt the business as little as possible. You can apply this process to a variety of changes, including those to existing procedures/processes, equipment, personnel, and more.
[Check out our full guide to the change management process for a more in-depth discussion].
The primary goal of change management is to prevent changes within an organization from negatively impacting safety, productivity, and quality. And in the food industry, there are so many ways to use this process for your benefit.
Examples of change management in the food industry
Food production processes include a wide range of variables—from regulatory requirements to packaging design. And that’s why companies in the food industry need change management: to coordinate any number of changes to these variables.
Here are some of the many ways that you can use the change management process in food industry processes.
Product packaging and labeling
Product packaging is one of the most dynamic elements of any food product. You might need to make packaging changes when:
- Seasonal items go out to market.
- Nutrition information changes because you’ve modified the recipe.
- The marketing team has decided to redesign the product.
- Regulatory agencies change their labeling requirements.
- You want to change how you load and ship items—leading to a packaging overhaul.
Having a change management process in food industry operations gives you full oversight of these modifications. And that’s essential if you have a large product offering or plan to expand in the future.
What this process does is implement a standard for requesting, approving, and implementing changes. Take the example of a marketing package redesign. Under change management, here’s a rough idea of the steps they’d take:
- Fill out a change request.
- for the request to be approved or denied.
- If approved, go through a review process of the implementation plan.
- Take all the actions outlined in the implementation step.
- Submit the change for final review and approval.
- Roll out the packaging change sitewide.
This standard process means you won’t struggle to keep up with the quantity and status of requests.
Ingredient suppliers
Another significant change that you’d need to coordinate is switching from one supplier to another. A simple workflow is all you need to ensure that all documentation is properly signed, collected, and filed.
It can also help you coordinate the downstream effects of onboarding a new supplier. This is especially true for ensuring accurate allergen labeling and product handling procedures.
Manufacturing change management processes
It’s essential to keep tabs on any changes to your manufacturing processes, things like:
- Health and safety protocols
- Food handling practices
- Equipment maintenance and inspections
- Product transportation
- Storage of ingredients and finished goods
- Introduction of new equipment like tools, PPE, etc.
Any modifications that may impact health and safety, productivity, or quality in a major way should be carefully executed.
Food safety and production equipment
At each step in the food supply chain there are many pieces of equipment workers must use. In the production environment you have things like forming machines and conveyor belts to manage. During the transport stage, there are refrigerated trucks, pallet jacks, forklifts, and more.
And when you introduce new, complex pieces of equipment into the fold, you increase the risk of safety incidents or contamination events. The management of change process ensures that any equipment related to a change is accounted for during the implementation phase.
Benefits of monitoring changes in food industry
In big organizations, it’s easy to see how the change management process provides value. With multiple facilities or lots of products, there are often too many moving parts to track everything by hand.
A manual approach almost certainly ensures that something slips past the safety and quality controls.
So, for large food companies, having a standardized approach to change management helps fill in the gaps and provides checks to prevent oversights.
But you can benefit from this process even if you only manage one facility or only have a few products. This is especially true if you plan on expanding in the future. Think about it:
How much easier would it be to implement a change management process in food industry operations before you start making any products?
Investing in this process now can save you potentially thousands of dollars in the long run—given the cost of safety incidents and product recalls. One of the best tools out there to implement change management in food industry operations is MOC software.
The Frontline change management software solution
Our change management software, Frontline MOC, helps companies in the food industry coordinate all the major changes happening around their operations.
It provides a standard workflow for your team to follow, so you eliminate variation in your approach to change implementation. There are four required and three optional steps in this workflow:
- Pre-Approval: Either approve or deny the change request.*
- New: Create a new MOC in the system (or start editing a pre-approved one).
- Evaluation: Perform an evaluation of the MOC and its potential impact.*
- Collaboration: Have a team of qualified individuals provide feedback on the MOC.*
- Approval: Approve or disapprove the MOC before starting work.
- Implementation: Complete all the tasks laid out in your implementation plan.
- Startup: Conduct a final review and initiate the full change.
* Denotes an optional stage in the workflow
Once your team completes a change, you’ll have access to a full report of all the steps you’ve documented. You can view the summary of a change at any time from your completed MOC log. Here’s an example of what the summary looks like:
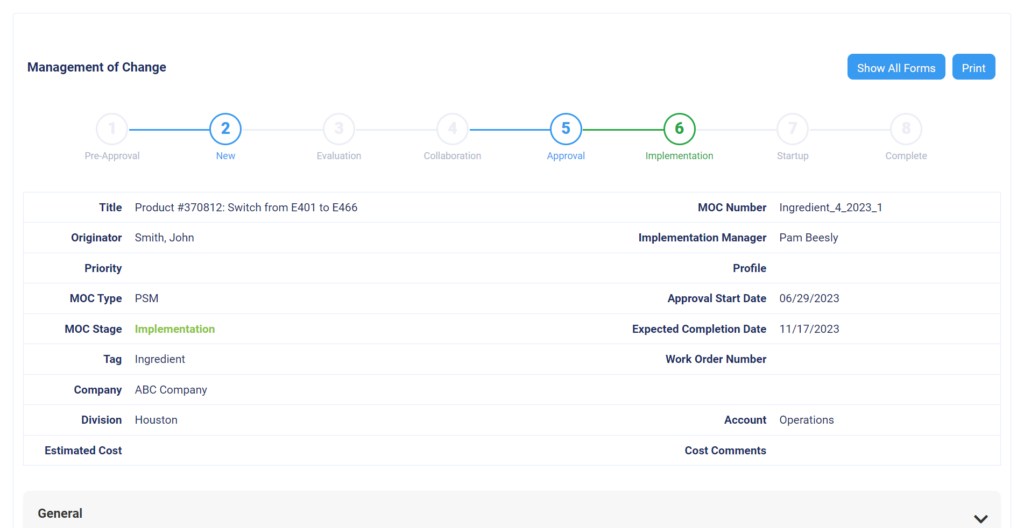
So, not only do you standardize how you implement changes, but you also standardize how you document them. This is ultimately a much more efficient way to oversee all the projects happening around your operation.