So, you’ve just been hired into a new company as the only person in the EHS department. Now what?
This might not be an issue if you’ve only got one location to manage and it’s not too big. After a few weeks, you should know your way around pretty well and be able to implement changes.
In this post, I want to share some of my similar experiences and offer you some advice on how to navigate working as a department of one.
How I ended up working alone
The most locations I’ve managed alone was 17 in total. When I first started at the company, there were 4 people in the EHS department covering 14 sites. We evenly divided the responsibilities between us so we could work effectively to cover each facility.
As time went on, some left due to personal reasons while others left due to job failures. A few years later, it became a department of one.
Surprisingly enough, during this time we actually reduced our incident rate by over 90%. We went from having an average of 30 recordable incidents per year to just two.
I don’t want there to be any confusion, though:
I was begging for help during this time without any resolve.
The company wasn’t doing well, and they essentially told me to just deal with it. So, I had to get creative on how I managed the EHS program.
Tips for managing everything
I take great pride in ownership of anything, and work is no different. I had to totally restructure our EHS program.
At this point, there was no longer anyone at the 17 sites doing the daily EHS activities needed to reduce incident rates, let alone progress our EHS program whatsoever.
So here are the steps I took to not only maintain 17 different locations, but also to help improve our EHS performance as a whole.
Identify each site’s needs
You can’t be everywhere at once. When you work in a department of one, you have to set systems up that run in your absence.
To cover multiple locations (or multiple departments in one location), I had to first figure out the EHS needs of each spot. That way, I could come up with specific control measures and requirements that would improve the safety of the area even when I wasn’t around to perform regular audits.
Collaborate with leadership
Another key to my success was partnering with site leadership to ensure the daily activities aligned with the performance goals. If, for example, you want to eliminate safety hazards in certain work areas, you have to make process changes.
But if you spend all your time addressing behaviors, you won’t be able to reach the overall objective. Make sure that your priorities and your actions are in alignment.
Set up monthly KPI’s
Speaking of safety goals, you have to track critical KPI’s in order to assess your progress. At my company, I set up a monthly safety meeting with each location to go over their data. During this meeting, we reviewed current performance and identified new areas of improvement that they could tackle.
Every month, I would send out an EHS report to senior leaders that included:
- Current performance metrics
- Action plans for improvement
- Goals and initiatives
Establish a safety committee
I firmly believe that every EHS department should have a safety committee. For me, because I was spread out across so many sites, the committee was made up of one representative from each location.
Having a mix of managers and frontline workers is a great way to form your committee. That will offer a broader perspective and can help you find solutions that work for everyone onsite.
Note: The committee members at each of my sites were given the title of “EHS Coordinator” and received a small incentive raise. These people completed EHS duties alongside their primary job function, so needed to be compensated accordingly.
Train site leadership in EHS topics
It’s unrealistic to expect that a single person can single handedly achieve the EHS goals for an entire site. Success depends on the participation of both managers and workers.
One of my top strategies was to provide specific EHS training to each shift manager. I trained them on things like:
- OSHA 30
- Hazard identification
- OSHA 10 (for the EHS coordinators)
- Site-specific EHS topics/goals
Having knowledgeable managers made it easy for me to feel confident leaving areas of the EHS program alone. This helped me prioritize those areas where I had zero support to lean on.
Schedule compliance tasks
I couldn’t have survived by myself without a detailed compliance calendar. It’s essentially a system to schedule and track the completion of regulatory requirements and other critical tasks.
I’ve found the best way to do this is in your EHS software system. You can set up recurring tasks, assign things to different people, and keep visibility over everything so nothing slips through the cracks.
Provide support and resources
Even though you may only be one person, you’ll probably serve as an EHS resource hub for your site/company. It’s important to be available for safety-related support (especially if you have multiple locations).
As the EHS specialist, you’re the one with the skills and knowledge to help with safety-related issues. Make yourself seen by traveling to different departments or entire locations on a regular cadence. That way, you give people a chance to ask questions and provide you with invaluable feedback.
Remember things don’t happen overnight, and they do tend to take time. So, if you’re an EHS department of one, give yourself some grace and take the time to create a strategic plan. Your company depends on you for a safe work environment, and you have to be able to advocate for your needs—even if hiring another EHS person isn’t an option.
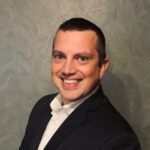
Jason Hathcoat
Jason is a seasoned EHS professional with more than 17 years of experience working in health and safety. He currently works as an EHS manager for a large global HVAC company.