I’ve seen a lot of training fails in my career. Training employees is a major component of every EHS program. As EHS professionals, it’s our responsibility to ensure that everyone is trained properly. And the word “properly” has turned into a subjective term within many companies.
Depending on who you ask, however, certain areas are considered nonessential. Below, I share the top three areas of training where people fail most often and how to avoid these failures yourself.
Irrelevant training content
The first area of training to address is the relevance of the content for the work your employees perform. For so many years, employers have either purchased or made generic training that doesn’t speak to the process at hand.
I used to work at a pipeline construction company. The new hire orientation consisted of a vertical commercial construction safety video that somebody bought from a popular generic training website.
I asked the employees: “What do you guys think of the training?”
Well, no surprise that they didn’t really learn anything that helped them with their jobs.
Something important to remember is that each process is unique to that company and its products. Just because you work in construction and you buy a construction training video doesn’t mean that it will align with your processes and procedures.
Avoid this common training fail by tailoring your critical safety training materials to the specific processes your workers do. Not only will this improve their experience, but it will also help make employees more confident and productive.
Insufficient content for regulatory compliance
The next area you should focus on is having the training that’s compliant with the federal and local regulations for your industry.
I once saw a forklift (PIV) training program that only included classroom instruction.
I said to the managers: “So, do your employees do any hands-on practical training?”
They replied: “Oh yeah, they do but we don’t document that. It’s too much work.”
There are certain areas of training which should include more than just the classroom part of the training. You need to know that the employee can safely operate the equipment or tool, and you can’t do that with a video and a paper test.
Another lesson to learn from this example is that you should be documenting all the training you do. For regulatory purposes, having detailed records is essential if incidents occur. You can only prove you adequately trained the employees if you documented it. In regulatory situations, it’s not what you did but what you can prove that you did.
Global harmonization system (GHS) training fails
I want to expand on this compliance point by quickly mentioning GHS training.
Many employers mistakenly believe that if they simply keep all their SDSs onsite and train their employees where to find and how to read them, that they’re compliant with GHS requirements.
In fact, however, there’s more to it than that.
Employees should know the dangers of the materials they’re working with on your sites. Which means, you need to teach them protective measures to take against those hazards/materials.
I’d highly advise you to train your employees in each individual chemical they’re dealing with. How would you possibly do that? My answer is to try and possibly merge them into your toolbox talks.
Poor comprehension and retention
The last area I recommend you look at is the retention of all the content you teach your workers.
First off, make sure you’re delivering training in the language that your workers understand best. If you train someone in their second or third language, you’re only checking a box. And this can cause serious safety hazards for the employee and their coworkers.
One way you to get around this issue is to require all your employees to be proficient in English and require a language assessment prior to employment. If you go that route, definitely run it by your legal department and HR to make sure the screening process complies with labor laws.
Regardless, I would plan on having your training available (in some format) in all languages which your employees have as their first language.
Do what you can with what you have
I know that some of these suggestions are difficult to implement if you’re at a company where they don’t currently exist. But there are always ways to adapt to the variables at hand to avoid training fails.
In my experience, making these kinds of improvements is way easier with the help of upper management. You’ll need everyone on board to successfully revamp the training program—HR, upper management, and floor managers.
And, of course, these are only a handful of the ways you can improve your site’s training approach. If you don’t know where to start, go to the source! Talk to your workers, do comprehension tests, and figure out the areas of your training program that need more work.
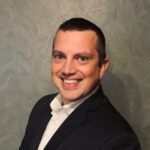
Jason Hathcoat
Jason is a seasoned EHS professional with more than 17 years of experience working in health and safety. He currently works as an EHS manager for a large global HVAC company.