As a seasoned EHS professional, it always drives me a little mad when companies set the goal of having zero safety incidents. The people and organizations who set these unrealistic goals don’t understand this concept:
Achieving zero safety incidents should not be the goal of an EHS program.
You might be thinking this sounds crazy. And from the outset, I might agree with you. But setting this kind of target can make it harder to protect workers from hazards. To understand why, it’s important to reflect on the history of corporate safety compliance first.
The origin of corporate EHS programs
In the United States, workplace safety standards didn’t materialize in a significant way until the early 1930s. In 1970, President Richard Nixon signed the Occupational Safety and Health Act into law, effectively leading to the creation of OSHA and modern work safety standards.
Before OSHA came along, there were no widespread safety standards. And company policies often prioritized productivity over worker health and safety. Workplace injuries and fatalities were rampant, and there were few laws holding companies accountable for these incidents.
Modern safety laws, however, center around a very simple idea that I wholeheartedly agree with:
Companies have a responsibility to protect their workers from health and safety risks.
But the problem with safety laws, like any other legislation, is that they often have unintended consequences. In the EHS field, OSHA standards have positively affected safety outcomes. But they’ve also led to a “pencil whipping” culture that treats safety as a regulatory burden.
Checking the boxes
In my experience, there are many companies today that view safety as a nuisance. These companies often appoint someone at random to be the site’s Safety Representative. Many times, EHS leaders are people who started out in other areas of the company (think: maintenance managers, operations leaders, HR professionals, etc.).
Then, senior leadership sets arbitrary goals for the EHS department, including having zero safety incidents. They emphasize a disciplinary strategy for achieving zero incidents. This then creates a situation where workers are afraid to express safety concerns and EHS professionals focus on looking good from the outset rather than making meaningful improvements.
When you allow zero room for error, you create more stress without implementing a solution. As an EHS veteran, I can think of several reasons why the zero-incident goal should not be your primary focus.
Reasons not to focus on zero safety incidents
If you’re focused on having zero incidents, then you aren’t focused on figuring out why incidents happened in the first place. Think about it: if your only goal is to have no accidents, you’d spend all your time babysitting workers.
That’s because humans make mistakes. The only way to ensure mistakes don’t cause incidents is to watch workers like a hawk and correct issues in real time.
You also need to think about how the zero-incident mentality affects workers. If you have no tolerance for safety incidents, workers will be far less likely to report hazards and near misses.
This robs you of the opportunity to investigate near misses and find new areas of opportunity. You’ll most likely miss the incidents because employees don’t want to negatively affect safety goals. I’ve seen some companies who do focus on this and there’s usually a lack of incident reporting as a result.
Instead, focus on realistic KPI’s like:
- Near misses reported
- Action item closure rate
- Number of completed inspection
- Safety concerns reported.
These KPI’s represent leading indicators that will help you encourage employees to engage with EHS programs while also targeting incident rate reduction.
Instead of fixating on how to have zero incidents, understand that incidents are always possible and that it’s better to focus on prevention than total elimination. By doing so, you’ll foster a positive work environment where employees feel comfortable reporting hazards before they cause injuries or worse.
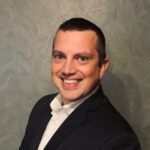
Jason Hathcoat
Jason is a seasoned EHS professional with more than 17 years of experience working in health and safety. He currently works as an EHS manager for a large global HVAC company.