Investigating operational issues is essential if you want to lower your risk exposure. To do that, you need to carefully review all problems, big or small, that have the potential to impact performance in a major way. Creating corrective action reports will help you improve your incident prevention measures and internal documentation standards.
What are corrective action reports?
Corrective action reports (CARs) are documents that explain what actions a company takes to address an issue. They can cover all sorts of operational issues, including (but not limited to):
- Safety incidents and near misses
- Environmental contamination events
- Product defects
- Safety recalls
- Production slowdowns or stoppages
The purpose of these reports is to fully document how your team responds to an issue. Not only is this useful for regulatory compliance documentation, but it’s also helpful for internal reflection. The more you document, the easier it is to learn from past successes and failures.
How to write a corrective action report
Like all recurring documents, writing a corrective action report is easiest when you use the same format every time. The general components you should include in your reports are:
- Description of the issue
- Detailed root cause analysis
- Corrective and preventive action item log
- Continuous monitoring
Let’s look at each of these sections in more detail.
Issue description
All corrective action reports begin with a full description of the issue at hand. In this section, you want to provide as much detail and context as possible. Anyone reading the report, regardless of whether they know the process or facility, should be able to understand the problem.
Root cause analysis
Next, you want to share the results of your root cause analysis. Oftentimes, there is more than one underlying root cause, so make sure to include all your findings here. This section is important for tying each of your corrective actions to a specific cause.
Corrective and preventive action item log
The bulk of the report describes, in detail, your corrective and preventive measures. Use this section to provide a complete account of all the things you did to address the root cause(s) of the issue.
Here are the questions to answer in this section:
- What did you do to respond to the immediate fallout of the problem?
- What was the purpose of each action item and which root cause did it address?
- Who oversaw the completion of corrective actions?
- What is your team doing to prevent the issue from reoccurring?
In the future, the details in this section may help you avoid solutions that failed in the past. Give a full account so that you can refer to this information later if necessary.
Continuous monitoring
A comprehensive corrective action report should include the outcome of your efforts. And it should also explain how you will continue to monitor the corrective measures moving forward.
This section should give an overview of how you’re measuring the effectiveness of the action items. Examples include performing weekly inspections, comparing incident data from one timeframe to another, and collecting quantitative data. Whatever your approach, just make sure it’s measurable.
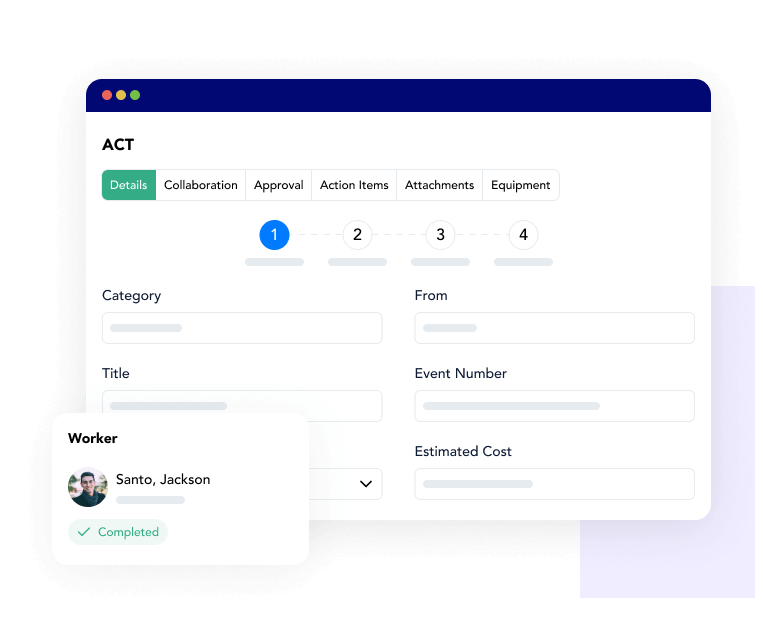
Reasons to document corrective actions
Excellent documentation is the key to top-notch EHS performance. Without it, it’s nearly impossible to stay on top of regulatory requirements, let alone make improvements. Here are the top five reasons why you should create corrective action reports:
- It lets you grow from past failures and make continuous improvements to your operation.
- It allows you to provide evidence of corrective actions in the face of litigation or regulatory citations.
- It fosters a proactive approach to operational performance areas like safety, quality, customer satisfaction, and productivity.
- It helps you lower risk exposure by decreasing the likelihood of recalls, safety incidents, and rework.
- It gives greater transparency to your incident management process and can help you refine your approach over time.
Advice for managing reports
Once you’ve figured out how to write corrective action reports, it’s important to decide how you’ll file and manage them. The best way to do this is with incident management software. All you have to do is upload or create your reports directly in the system. Software makes updating, organizing, and browsing current and past reports much easier than a manual process.
If you don’t have software, then the next best alternative is to store all your reports digitally. File management is key to being able to find and review past reports. I’d recommend including the incident type, date, and unique identifier in the file name. That way, you can organize them by date even if they get updated later. Here’s an example of a file name to use:
Recall_ProductB3Q 2050-01-15
If you use the same syntax each time, it should be easier to manage your documents. That’s good advice for incident management as a general practice. Maintaining a consistent approach is essential for becoming effective at incident response.
Overall, creating detailed corrective action reports and making them accessible is a great way to improve in all areas of performance. Use these documents to learn from your successes and failures, so you can reach your goals and become more efficient as a company.