Operational changes can wreak all sorts of havoc on business performance if you don’t manage them properly. The best way to standardize change management is to implement a software system like Frontline MOC. Not only does it improve communication and increase visibility for changes, but it also prevents major failures and ensures careful documentation.
Why do you need to standardize change management?
Change management plays a critical role in the safety and success of any complex system. In chemical manufacturing, for example, unmanaged changes pose a significant safety risk to workers and the communities surrounding processing facilities. That’s why, for example, OSHA included change management in its process safety management (PSM) regulation—to prevent accidental chemical releases and the dangers they pose.
If you don’t standardize change management, you simply can’t guarantee the safety of a change. That’s because you won’t be able to properly trace back its origins and understand the cause of issues or setbacks. In industrial settings, there’s a potential disaster in waiting for risks to grow before you revisit your strategy. Having a process to approve, plan, implement, and verify changes allows you to identify risks in real-time rather than after they cause a problem.
It’s more than just having a process in place, though. For long-term success, your team needs to be consistent. And if you don’t have a way to oversee the status of each change, then it’s hard to know where you stand. Inconsistency, over time, causes you to overlook hazards and underestimate risks, leading to even higher stakes.
When you standardize change management, you gain more control over the outcome. Being able to hold your team accountable keeps projects on track and ensures that documentation meets company standards.
Common change management questions
These are the most common questions we hear from potential clients on how to standardize change management.
How do you manage planned and unplanned changes differently?
In industrial environments, factors like employee turnover, market conditions, supplier issues, weather, and contractors can cause unexpected issues. This doesn’t even include the variables within your control—things like training, health and safety, and process efficiency.
Examples of planned changes
- Routine equipment maintenance
- IT system upgrades
- Employee onboarding and offboarding
- Product rollouts and updates
Examples of unplanned changes
- Replacement of broken parts or components
- Corrective action following a safety incident
- Employee offboarding
- Product recalls
- Environmental incident follow-up
The biggest factor separating these types of changes is time. With unplanned changes, you don’t have as much time to prepare and analyze your strategy. That’s why having a formal MOC process in place is so important.
When unplanned changes happen, an effective MOC process gives your team the structure to respond effectively and reduce the total impact of the issue.
How do you keep stakeholders informed about changes?
Keeping everyone updated on changes is challenging—even for teams with excellent communication. But it’s a very important part of the change management process. While some changes might only affect a single department, others may affect:
- Multiple departments
- Suppliers and vendors
- Customers
- Frontline employees
- Contractors
- Local communities
Trying to keep everyone updated via email is a common but highly ineffective approach. For critical changes, email makes it harder to collect and review feedback, address concerns, plan, and assign and track tasks.
Without a central system to coordinate changes and communicate about them, key decision makers might miss important deadlines or steps in the process. MOC software prevents these issues by providing a detailed log of what’s happening so everyone stays engaged and informed.
How do you track the outcome of a change?
Implementation should never be the last step in your MOC process. You need to track changes afterwards to make sure they’re safe and effective, especially if they’re long-term ones.
Analyze results: Did the change accomplish what it was supposed to?
Collect feedback: What do employees, customers, etc., think about the change?
Monitor performance: Is the effectiveness of the change long-lasting and sustainable?
Adjust accordingly: What adjustments do you need to make to the strategy?
If you don’t standardize change management, it’s highly unlikely that you’ll know the long-term performance of your strategy.
What information should you document for operational changes?
It’s hard to manage changes well if you don’t document them properly. In high-risk work environments, poor records management can cause all sorts of problems—from noncompliance to dangerous mistakes and oversights.
Here are some key pieces of information you should record:
- Detailed description and intended outcome
- Reason for the change
- Severity and risk level
- Equipment affected by a change
- Approval and signoffs
- Implementation process steps
- Analysis of the change
- Corrective actions
You should also keep all the permits, licenses, contracts, and other documents related to the change organized. Until you verify and close out the change, it’s good to have access to all the information that went into it. Plus, it comes in handy if there are compliance or performance issues down the road.
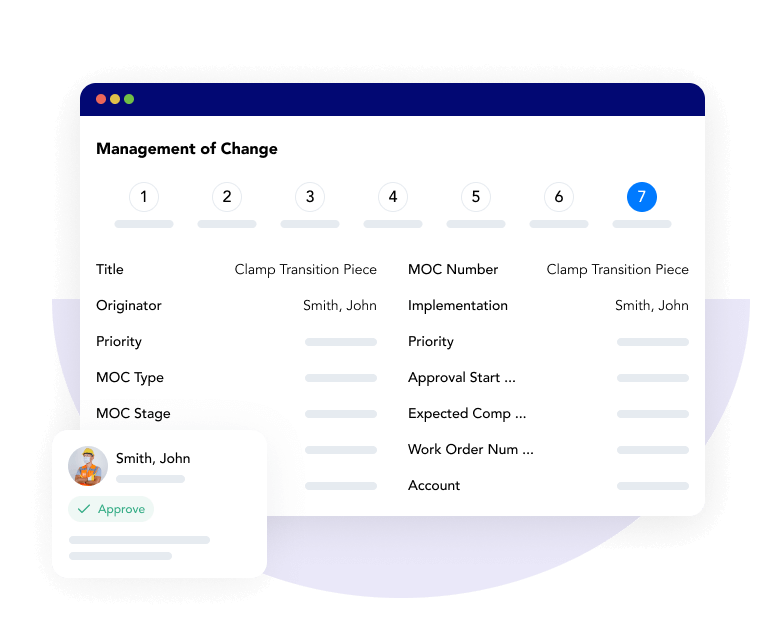
Why informal change management rarely works
It’s common for teams to view small changes as too insignificant for a dedicated strategy. A good example of this is making minor equipment changes that seem to have no impact on the safety or functionality of the process. Your employees might make these changes without consulting you or documenting anything, and oftentimes there’s no visible impact. But every change, regardless of size, has a cost.
These are some of the ways unmanaged changes impact your operation.
Impact on resources:
- Spend more time tracking down people to complete tasks, approvals, signoffs, etc.
- Require more people to document and implement a single change.
- Invest in more and more tools to try and fix communication, documentation, etc.
Effect on cost:
- Complete more rework and produce more scrap due to poor planning or execution.
- Delay the implementation of the change and reduce its overall effectiveness.
- Make mistakes that cause unplanned downtime, material costs, and more.
Impact on compliance:
- Underestimate risks that cause compliance gaps and lead to audit failures.
- Miss critical tasks that lead to safety incidents, training gaps, etc.
- Fail to meet regulatory requirements for documenting operational changes.
At least in heavy industries, most changes pose risks to health, safety, quality, productivity, and other areas of performance. Trying to coordinate these projects via email, spreadsheets, paper forms, and undocumented conversations exposes you to more unnecessary risks.
The benefits of investing in MOC software
If you already have a decent MOC process in place, you might not see the immediate benefit of using software. But don’t forget that a lack of incidents isn’t always an indicator of great performance in health and safety. In fact, it’s possible that your next major incident is just around the corner, and you don’t have the oversight you need to prevent it.
Investing in MOC software closes the loop so you can be confident in the quality and efficacy of your operational changes. And the benefits of it extend beyond safety.
Reasons to consider software
Here are some of the main reasons why you should seriously consider change management software for your team.
Improved EHS performance: The more effectively you manage changes, the lower your risk of incidents and noncompliance.
Fewer process errors: Software gives your MOC process structure, meaning that employees are less likely to make errors or miss critical deadlines.
Less administrative work: Systems like Frontline MOC have built-in reporting and documentation functions that eliminate many administrative change management tasks.
Centralized MOC process: Coordinating changes in a software system means you don’t have to look in a hundred places for the information you need.
Better process outputs: Having a detailed paper trail allows you to analyze the success of your changes and come up with more effective solutions in the future.
While software is a powerful tool to guide your process, it’s not a magic fix. Successful change management requires you to set and enforce standards for communication and documentation.
Software does, however, free up your time so you can complete more changes with better results over time. That means your operation will run smoother and have a lower overall risk level than if you try to complete everything manually. The long-term impact is fewer costs related to administrative work, process inefficiencies, and incidents.
Coordinating changes with Frontline MOC
Whether it’s a regulatory requirement for your operation or not, management of change is an essential process for controlling risk. With an informal or manual strategy, it’s hard to oversee what your team’s doing. Information gets scattered between meeting notes, emails, personal conversations, paper forms, etc., and you lose visibility. That’s why companies use change management software to set up their process and maintain oversight.
A user-friendly system like Frontline MOC standardizes change management by requiring teams to follow a specific workflow each time. Within the system, your team can:
- Request changes
- Approve or deny requests
- Assess the severity and risk level of potential changes
- Create, assign, and track action items
- Coordinate implementation
- Review upcoming and past changes
- Document the entire process
The main benefit of using MOC software is that it fills gaps in the process. It means that you don’t have to rely solely on excellent communication. Instead, you can use the system to get instant updates on all the work that’s done or upcoming to approve, plan, and implement a new change.
Whether you’re installing new equipment, restructuring your organization, onboarding employees, or anything in between, change management is a necessary process to follow. It will lower failure rates, reduce risk, and ultimately help the operation run more efficiently for long-term success.
Other posts you might like…
No posts