We sat down with Kamryn Johnson to uncover what proactive safety in manufacturing looks like. His experiences highlight the need for a collaborative approach that treats frontline workers as partners in incident prevention.
About Kamryn Johnson
Kamryn Johnson is an EHS Manager at Kalas Manufacturing Inc. In this role, Kamryn helps oversee health and safety operations for the manufacturing and distribution of wire cable products.
After becoming a certified forensic interviewer (CFI), he started doing field interviews for incidents, injuries, accidents, and quality RCA’s. Since then, Kamryn has worked in manufacturing operations for construction, oil gas, and many general industry facilities. He’s led multi-location/multi-state manufacturing programs as well.
Kamryn’s focus is on restorative EHS with the purpose of rebuilding EHS programs from scratch or implementing programs at sites that do not have one. He still travels regularly throughout the US to consult with manufacturers and conduct development sessions with EHS professionals.
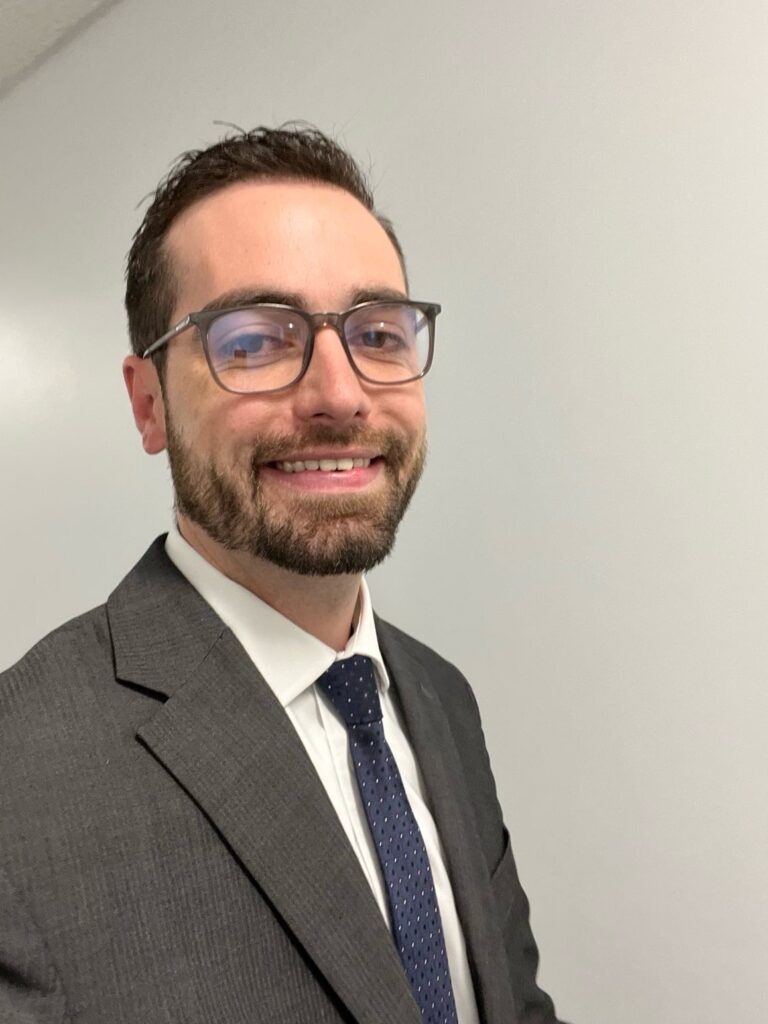
Proactive Safety in Manufacturing
Kamryn got into EHS after working in risk for a few years and seeing the data on the impact of safety failures. From there, he realized that he wanted to help companies mitigate risks and avoid compensatory incidents. With more than 7 years of consulting experience, Kamryn has gathered all sorts of insights on what it takes to practice proactive safety in manufacturing.
1. In your experience, why do manufacturing sites fall into reactive safety mode, even if it’s the intention of senior leadership to take a proactive approach?
I believe if senior leadership expects a proactive approach, but a manufacturing site is in a reactive mode, there’s gap somewhere. That could be at the employee level, supervisor level, or manager level. Somewhere there’s a distortion of expectation.
I see this often when the operational need or expectation is greater than the perceived expectations around safety. Also, this happens if the intention is proactive, but the site is tracking lagging metrics like days safe, DART rates, etc.
I also believe many facilities fall into a reactive mode due to calculated risks. They’re operating in an environment with a higher potential for injury and become numb to the day-to-day environment. A good example of this is when teams don’t do near miss reports or hazard identification reports because they view these near misses and hazards as just part of the job.
To get out of this mode, I’d really recommend taking a step back and making sure that:
- The metrics you’re tracking are appropriate.
- The expectation of safety is clear top to bottom and bottom to top.
- Your team understands the difference between a working hazard (e.g., fall protection) and a preventable hazard (e.g., PIT near miss).
2. If you were evaluating a manufacturing facility, what would you look for to determine the quality and effectiveness of their safety program?
While consulting, I would look at three things to establish a baseline of the current state of their program: consistency, education, and discipline.
Consistency
The first one is consistency. Do they have consistency through the leadership team? Is the message that’s going down the chain or up the chain established and clear? Is that message shared consistently? Some common phrases I hear are:
“This is the way they will tell you that you need to do this, but this is how I do it.”
“You should wear a hard hat at all times onsite, but I really just wear it when I’m working near the machines.”
From the corporate side, I often hear stuff like “I have some great ideas, but there’s no EHS budget, so I haven’t gotten any of them approved to try yet.”
This lets me know there’s inconsistency in the strategic direction, expectation, and accountability surrounding the safety program.
Education
The second thing I’m looking for is education. What information is leadership passing to frontline workers? Are these workers aware of the hazards around them? Do they have the training to do their job safely? This can span from MSDS knowledge to machine guarding, fall protection, TSCA/RCRA, PPE, etc. One key way that employees put themselves in compromised positions is to not understand the hazards associated with the task they’re performing.
Discipline
The third thing I’m looking for is discipline. If I arrive to a site to conduct an assessment and disciplinary action is the main way they handle safety, I usually conclude that there’s a gap (sometimes substantial) in the safety program.
I’m a huge proponent that safety should not discipline anyone, ever. EHS is there to consult, mentor, develop, and lead the teams they work with, but they should never be involved in discipline.
I have a book coming out in 2026 on these principles (plus another, engagement) and how they can transform your site’s safety culture. Keep your eye out for that!
3. Can you give an example of an operational change you (or someone you know) has made to take a more proactive approach?
I implemented QR code reporting for employees at multiple sites which allows for quick, effective, and, if they want, anonymous reporting of employee safety concerns. From that, I’ve seen an increase in hazards, concerns, and employees’ offering solutions to problems they see. In one case, the rate of hazards reported was almost five times higher than with prior reporting methods. Plus, the quality of the reports improved.
Employees appreciate not having the pressure from supervisors when making their reports. They also like how simple and convenient it is to fill out the form from a QR code.
Having a QR system has helped us understand safety issues directly from the team and get ahead of potential incidents. It has also empowered our employees to engage in the incident prevention process by giving them a voice.
4. In your opinion, what are the leadership qualities EHS professionals should develop to get their team more involved in incident prevention?
As the saying goes, “they will not care how much you know, until they know how much you care.” I think EHS professionals should focus on leading, coaching, and mentoring instead of enforcing. Most teams need constant development. Mentoring your EHS team will shift the employee perspective from “EHS is the safety police” to “EHS cares about us.”
If frontline workers don’t trust the EHS team, they won’t want to report near misses, minor incidents, or even minor compensatory accidents. Being proactive with incident prevention builds trust between your department and the workers.
One time, I saw a safety manager tell their team: “It’s not about discipline, I just need to know who did it so I can figure out why. This will help me make sure it doesn’t happen again.” The workers who did it spoke up and received a write up later that day. Do you think they’ll want to be proactive or work with the safety team in the future? What about the rest of the team who saw this situation play out?
5. Do you have any tips for reinforcing proactive behaviors and rewarding workers who practice them?
My top tip is to build a program that gets employees talking about safety every day, not just once in a while. If you can incorporate incentives based on repetitive acts, it’s a win-win.
My favorite safety incentive program is a swag program. Basically, we give workers fake currency for consistently following safety rules over time. They can either save up for bigger items like coolers or headphones or spend the money quickly on small stuff like cozies or T-shirts. In the beginning, a lot of workers join the program just for the rewards. Over time, though, I’ve seen it develop into open conversations about safety.
At one company, we spent $20,000 on this program in the first year but mitigated 18 compensatory injuries from the prior three years. The estimated cost avoidance of going from 28 recordable incidents to 10 was nearly $270,000. In the program’s second year, they went from 10 recordable incidents to 2, spending another $15,000 on the program. Since then, there have been less than five recordable incidents per year. And while I can’t say for sure that the incentives program caused these results outright, it definitely has helped me develop proactive safety in manufacturing teams for the long-term.
6. What’s your advice for an EHS specialist who’s experiencing a lot of pushback from employees and wants to get them to be more proactive about personal safety?
In my experience, pushback tends to come from a few areas. I’d start by figuring out why employees are pushing back. What does employee engagement currently look like? Is this coming from the office or boots on the ground? Are we giving employees a voice? When it comes to personal safety, do employees have the training and knowledge to report concerns? For example, just asking them to report unsafe work conditions is not enough because everyone has a different definition of what’s unsafe. Not everyone knows the hazards around them until someone points them out.
A great example of this is the time I completed a facility risk assessment and determined that everyone should be wearing eye protection. When the news got out, there was an uproar. The workers had never worn safety glasses in that facility before. There was an average tenure of 15 years in the building.
After going back to the facility and discussing with the team, I held a meeting with all of the employees and went over the risk assessment step by step with them. We talked about the current layers of protection, the hazards identified, and the result. I listened to their questions and frustrations. By the end of the meeting, each employee understood and agreed that they should be wearing safety glasses. A few of them switched directions to saying “we should have been wearing them this whole time.” I even had a few associates ask if they could help pick out the glasses the facility would offer.
Remember, workers aren’t always irrational with their resistance to policy. They draw conclusions based on their experience and if you want them to get on board, make sure you take the time to engage them in the process.
7. In your opinion, what are the main things EHS leaders can do to achieve proactive safety in manufacturing environments?
My approach is based on the four principles I mentioned earlier: consistency, discipline, education, and engagement. You need to identify inconsistencies, avoid a disciplinary approach, educate your team, and engage workers to form a proactive strategy. If you have any questions about this, you can reach out to me on LinkedIn and check out my book when it comes out in 2026!
Kamryn’s Resource Recommendations
We asked Kamryn to share how he stays active in the EHS community and up to date on regulatory requirements.
EHS Professional Resources
I’m registered with most of the regulatory agencies for email updates on regulations. I’d recommend checking out Safety Knights, too. It’s an online community dedicated to EHS professionals that’s more focused on communication, development, and linking mentees with mentors in the EHS field.
Advice for EHS Professionals
“Focus on integrating your EHS strategies, goals, and objectives into the overall business strategic plan. Doing so will obtain more top leadership support and align on directional thinking.”
Other posts you might like…
No posts