The disaster in waiting to invest in your EHS program
Have you ever wondered why some companies have a very robust safety management system while many others have a very basic, bare bones approach? Why do some companies “pencil whip” policies and inspections while others actually drive leading indicators to change the culture?
From the outside looking in, it would almost appear to many people that some companies truly care about their employees’ safety while others only care about the money. Have you ever wondered what the difference is between these companies?
Every company cares about making money, right? So why do some invest in their EHS programs while others just do the bare minimum requirements to remain compliant? What does compliance even mean anyways? Can a company truly be 100% compliant? Well, that’s an entirely different discussion for another time.
Changing how you view safety
We’re finally getting out of the worldview where we (EHS professionals) are viewed as the “bad guys,” or just something I like to call a “window decoration.”
To me, a window decoration is any EHS professional who exists solely for a company to be able to say they have someone in that role. This pertains particularly to companies who view the EHS department as an optics play, using it purely to look good for customers, investors, and partners.
Usually, these companies are the ones who’ve been lucky enough not to experience a catastrophic event for which they were responsible.
Because most (not all) companies who have gone through a major incident tend to implement a decent EHS program afterwards.
So, my question, my challenge, to the companies who are lying in wait until some major incident happens is:
Why are you waiting?
Why can’t you see that you’ve been lucky so far and that you’re likely to fall off the “luck train” at any moment?
I can tell you this—most EHS professionals want to be more than just some window decoration, and they don’t like working for companies that treat them as such.
These are the individuals who really want to continually change and improve the company’s approach to safety. These EHS professionals care about the well-being of their workers and want to empower everyone to take an interest in their personal safety.
The cost of inaction
My experience with these companies is that they don’t invest in the EHS department because they believe it costs too much money. They don’t want to invest in it because they’re either not currently experiencing safety incidents or are unaware that these incidents are occurring.
Okay.
*Sighs*
Let’s break this one down:
An OSHA citation is, at minimum, $15,625 per serious classified violation. If OSHA can cite you for a willful or repeated violation, that number jumps to $156,259 (per violation). You can check out the penalty amounts here.
To make it more complex, if you’re also in violation of EPA regulations, you can see just how steep those violation fines are.
Then, add the cost of having just one medically consulted incident, which is $42,000 per injury (on average). If there’s a fatality that average cost is $1,340,000.
I worked for one company that didn’t really take safety as seriously as they should have, and it cost them a lot of money. There were nearly 30 medically consulted injuries per year…every year. The company was unknowingly spending about $1,260,000 per year just because they weren’t taking EHS seriously.
Finally, a lightbulb came on, and we changed a few things and reduced the count to just two injuries the following year.
Think about it this way: the money saved from not having injuries on its own was enough to cover all the EHS budget requests I’d been making and still have some left over.
Disaster in waiting for safety incidents to occur
I’ll spell it out plainly: top tier EHS professionals don’t want to work for companies who view safety as a nuisance and a drain on their resources.
Working for a reactive (versus a proactive) company poses a certain amount of risk to professionals who want to advance in their careers. No number of certifications can make up for the professional stagnation that happens while working for a company who doesn’t take safety seriously.
Failing to invest in safety has a cyclical, negative impact on performance.
When you don’t invest in safety, the EHS professionals who actually care about performance eventually leave. The ones who stay are likely those who aren’t truly invested in the well-being of your workers.
Over time, this degrades your EHS program and leaves you more exposed to major incidents and the expenses that come with them.
I’ve personally worked for both types of companies: those that care about safety and those that pretend to care just to satisfy their stakeholders.
There’s a level of disaster in waiting for major incidents to happen that goes beyond indifference. It’s a conscious decision to put your profits above your people, and time and time again this is proven as a losing business strategy.
If you think you’re invincible, let me tell you that you’re not. Just exactly what are you waiting for?
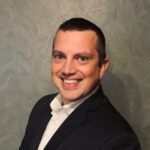
Jason Hathcoat
Jason is a seasoned EHS professional with more than 17 years of experience working in health and safety. He currently works as an EHS manager for a large global HVAC company.
Other posts you might like…
No posts