Manufacturing is one of the largest sectors contributing to U.S. economic growth and stability. But in 2023, there were 391 fatal manufacturing injuries impacting workers in this critical industry. To better understand manufacturing safety risks, we analyzed data from both OSHA and the Bureau of Labor Statistics (BLS). Read our report below to see our top insights!
Fatal manufacturing injury rate
One important indicator of workplace safety trends is the fatal injury rate. This metric is the number of fatal injuries per total hours worked by 100,000 full-time workers.
The rate of fatal manufacturing injuries was 2.5 in 2023, meaning that there were 2.5 deaths for every 100,000 workers. This was a 0.1 decrease from the 2022 rate of 2.6. Compared to other industries, the fatal injury rate in manufacturing is relatively low.
Here are some occupations where the rate is much higher:
- Agriculture, forestry, fishing and hunting (20.3)
- Natural resources and mining (19.5)
- Mining, quarrying, and oil and gas extraction (16.9)
- Transportation and warehousing (12.9)
- Construction (9.6)
Of course, manufacturing poses more risks than industries like education and health services, where the rate of fatal injury is less than 1 death per 100,000 workers. But regardless of how manufacturing compares to other industries, it’s always important to keep perspective. With nearly 400 deaths in 2023 alone, manufacturers still have much room to improve and protect their workers against safety risks.
Safety risks by subindustry
To fully understand fatal manufacturing injuries, we analyzed them by subindustry. The BLS organizes the manufacturing sector into 21 subsectors. Here is a breakdown of the fatal injury rates for nine of them:
Injury rates for manufacturing subindustries
3.0
8.5
1.2
3.3
10.0
1.6
5.7
4.4
5.1
As you can see, the most fatal subindustry is nonmetallic mineral product manufacturing. This includes production of minerals like clay and sand. When comparing subsectors, consider the location of the operation and type of equipment workers use. Variables like these have a major impact on safety risks. If uncontrolled, heavy machinery can quickly turn deadly in a loud, busy manufacturing environment.
Types of fatal injuries
Another data point we wanted to look at was the type of fatal injuries happening in production facilities. Here’s a breakdown:
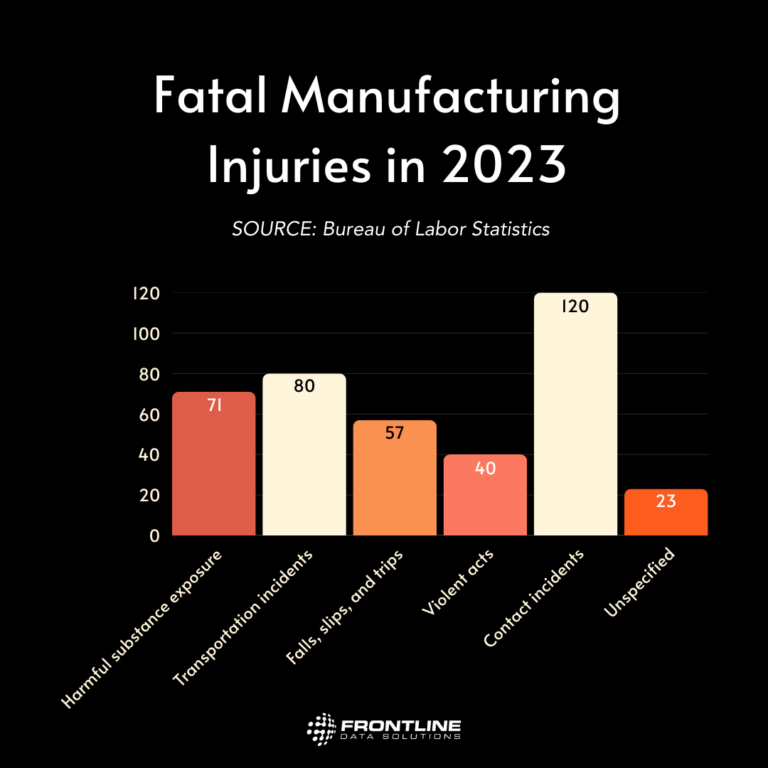
Of the 391 fatal manufacturing injuries that occurred in 2023, nearly a third came from contact incidents. A contact incident is when a worker sustains an injury after contact with a person or an object. Objects could be pieces of equipment, materials, structures (e.g., shelves), etc.
Another 20% of fatal injuries come from transportation incidents, typically involving forklifts, reach trucks, vans, and other driving equipment around manufacturing operations. Unsurprisingly, we found that the top causes of nonfatal and fatal incidents align very closely with each other.
Nonfatal injuries in manufacturing
While general manufacturing isn’t nearly the most dangerous sector in the U.S. economy, it has some of the highest risks for nonfatal injuries. In 2023 alone, there were more than 355,000 nonfatal injuries in manufacturing operations.
Of the injuries resulting in days away from work, the most common types of incidents were:
- Struck by object or equipment
- Caught in or compressed by object or equipment
- Fall on same level
- Overexertion in lifting or lowering
- Exposure to harmful substances or environments
These are broad categories compared to the variety of processes and equipment across the manufacturing sector. Depending on how you view the data, safety risks change drastically from one type of facility to the next.
Someone working in a chemical production plant might have a high risk of chemical burns. Meanwhile, a worker in the food industry might not encounter hazardous chemicals at all.
Insights from manufacturing incidents
From incident descriptions in OSHA severe injury reports, it’s apparent that manufacturing equipment is a major workplace hazard. In most manufacturing environments, heavy machinery plays a big role in safety outcomes. Processes like stamping, cutting, and molding materials often require the use of large equipment, and strict safety measures are necessary to prevent injuries.
Here are just some examples of injury reports involving manufacturing machinery (we’ve paraphrased these descriptions directly from OSHA’s database):
Example 1:
A worker was holding a load-out hose when the valve opened unexpectedly. The sudden release of pressure caused the hose to strike the worker and break their leg.
Example 2:
When a worker started up an extruder (a machine that melts plastic), a piece of the equipment detached and hit them in the leg. This resulted in a severe gash injury that needed medical attention.
There’s also no shortage of manufacturing injuries related to the work environment itself.
Example 3:
While removing unused conduit, a worker tripped over a spill containment wall that was one foot high. He fell and fractured his tibia and fibula.
Example 4:
A worker was drawing a sample from a digester when a hot copper sulfate solution from a different digester splashed onto their back. The solution caused third degree burns.
When it comes to preventing these types of incidents, it’s safe to assume that there are many variables at play. Successful EHS programs must continuously assess and account for manufacturing risks to ensure the effectiveness of safety control measures.
Even if the process, equipment, etc., doesn’t change frequently, there’s always the human element to consider. Employee turnover increases safety risks each time new workers come onsite.
With nearly 13 million workers, almost 4% of the U.S. population works in the manufacturing industry. Their safety is critical for our modern society to function the way it does. While fatal manufacturing injuries are sometimes the result of freak accidents, there is almost always a better control measure, a better policy, or a better process to prevent them.
Other posts you might like…
No posts