FSMA 204, the latest food traceability rule from the FDA, is designed to stop major public health outbreaks from occurring. With more detailed tracing and recordkeeping requirements, this rule builds on more than a century of American food safety regulation.
History of food traceability laws
The traceability of food products dates back to ancient civilizations like the Greek and Roman empires. But in the United States, food safety laws didn’t come into play until the early 1900s when unsanitary work practices became a larger topic of concern.
Under the Food, Drug, and Cosmetic Act of 1938, businesses began operating within stricter parameters. The FDA passed several more food safety acts between 1960 and the late 1990s, until the events of September 11th, 2001.
Following the 9/11 attacks, the US government saw the need for greater food safety and passed the 2002 Bioterrorism Act (BTA). This legislation addressed both intentional and unintentional contamination of consumer products.
Companies began submitting food tracing records sometime around 2004, marking the start of modern regulated traceability. These changes challenged businesses to create and implement detailed food safety plans, track their finished goods, and quickly identify contamination sources.
Less than a decade later, in 2011, the Obama Administration passed the Food Safety Modernization Act (FSMA) to usher in the next era of food safety regulation.
Widespread FSMA compliance
The FSMA expands on previous food traceability rules by focusing on preventing foodborne illnesses, not just reacting to them. It does this by outlining specific actions that businesses need to make at each point in the supply chain.
FSMA regulations also give the Center for Disease Control and Prevention (CDC) more authority to collect food traceability data. With an increased amount of data, the CDC can provide better guidance on the prevention of foodborne illnesses and recommend more effective safety standards as well.
Since its passing over a decade ago, the FSMA has established a modern food safety system for companies to adopt. A major goal of this legislation has been to repair the public’s relationship with food companies. Increased consumer confidence makes it easier for brands to establish a long-term position in the market as well.
Moving into the 2020s, a new rule aims to build on the public’s trust by creating greater transparency within the supply chain.
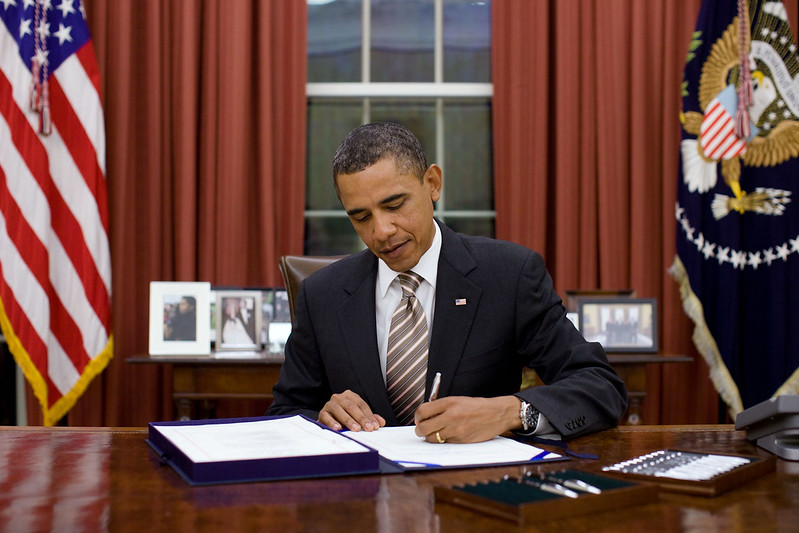
Food traceability under FSMA rule 204
FSMA rule 204 takes food traceability to new depths by looking at high-risk steps in the supply chain on a more granular level. This rule requires companies to keep detailed traceability records for specific events (known as critical tracking events), so products are easy to track.
Rule 204 is designed to:
- Make it easier to identify sources of foodborne illness.
- Reduce the time it takes to recall contaminated products.
- Bridge traceability gaps within the supply chain.
- Simplify the root cause analysis process when outbreaks occur.
Another benefit is that this rule will help satisfy consumers’ desire for increased product transparency from the food brands they support.
Requirements of the food traceability rule
Rule 204 applies to all the items found on the FDA’s food traceability list (FTL). Some examples of items on the list include fresh cut fruits and vegetables, finfish, and herbs. Under the rule, businesses will need to keep detailed traceability records for all foods that fall on this list.
In general, there are three major requirements of FSMA 204 that companies need to focus on:
Critical Tracking Events (CTEs): The growing, receiving, transforming, creating, and shipping of food products are considered CTEs. This means that any business involved in one or more of those areas of the supply chain will need to provide detailed traceability records.
Key Data Elements (KDEs): Depending on the CTE, there are required data points that must be included in records.
Traceability Lot Codes (TLCs): Each record must contain a lot code that helps identify the product.
There are no requirements for the type of technology used to keep these records, and this rule does not require businesses to provide a full pedigree for each product. However, there are several important guidelines that may heavily influence the recordkeeping system that companies use:
- Businesses must keep their records for at least 2 years.
- Records must be in a sortable electronic spreadsheet format in case of an outbreak.
- Businesses must provide the records within 24 hours of an FDA request.
- Records must be legible and in either electronic or paper format.
So, while businesses can choose a recordkeeping system, they’ll ultimately have to make sure it allows them to easily meet these data reporting and storage requirements.
FSMA 204 timeline
The FDA initially proposed FSMA 204 in September 2020, and it into effect in January 2023. Businesses have a grace period of two years to ensure compliance with the rule. This means that by early 2025, all businesses that fall under FSMA 204 will need to have adjusted their traceability protocols and recordkeeping systems.
Within the food and beverage industry, there has been much speculation whether the rule would become a requirement. Many have opposed the rule, calling it unnecessary given the other food traceability standards already in place.
Regardless of how they feel, however, brands need to start preparing now in order to meet the implementation deadline.
Getting ready for FSMA 204 compliance
The good news is that companies with a robust food safety tracing system in place should be able to meet FSMA 204 requirements without a major disruption. Most businesses will likely need to add traceability analytics to several areas of their process. And workers will need updated training to ensure widespread compliance (especially in companies with multiple facilities).
The easiest place to start is to consult the food traceability list for all the products and ingredients that fall under FSMA 204. After determining the products that fall under this rule, businesses should establish which key data elements (KDE’s) they’ll need to track. The FDA has a detailed page on KDE’s here.
Then, companies should assess their current recordkeeping systems to ensure that all KDE’s are included in the data collection process. Large operations will need digital tracking systems for their traceability lot codes (TLCs), product IDS, and other data points.
With the two-year grace period, it shouldn’t be a problem to reach FSMA 204 compliance. But the best practice is to start now and save yourself the headache of trying to implement detailed recordkeeping systems that meet FDA requirements at the last minute.