These days, achieving regulatory compliance (regardless of industry) requires a dedicated EHS program. These are the basic steps for how to implement a safety program that allows you to both achieve compliance and create a strong safety culture.
Do a preliminary safety audit
One of the hardest parts of EHS management is changing the status quo. Unless your facility is brand new, you likely have existing issues to address before you implement your safety program.
Start by auditing the current situation, and look for answers to questions like:
- Are there any formal safety policies already in place? If so, what are they?
- Aside from training, do employees receive any additional safety instruction?
- What is the senior leadership team’s attitude toward safety?
- What are the major areas of improvement you’ve identified?
- What components of safety take up most of your time?
These are just some examples of what you can explore during your review. Doing this preliminary safety audit will help you decide where to direct your focus.
Create your safety program plan
The next step is to come up with an implementation plan. My best advice would be to make a checklist of all the concrete things you want to accomplish but try to keep it as simple as you can. And that’s because you’ll need some flexibility once you start implementing a safety program. Here are some of the line items I’d include in your implementation plan checklist:
- Create a written health and safety plan.
- Conduct a job hazard analysis for each job title within the operation.
- Do a risk assessment of each process.
- Develop high-quality training content materials.
- Establish the training requirements for each role.
- Create a system for receiving and acting on employee feedback.
Assign and complete implementation tasks
Once you’ve got a plan, it’s time to start tackling the implementation tasks. I’d recommend assigning these to specific people so you can have accountability during the process. You should also set deadlines for different milestones to keep everyone on track.
Your safety program should start to take place around the action items your team completes. Piece by piece, the components will start to fit together until you have a working program in place.
Communication and follow-up
After you have a program up and running, it’s essential to communicate the details to both management and frontline employees. You should never assume that anyone’s paying attention to what your EHS department is doing.
When you introduce a new policy or procedure, put in the effort to communicate it clearly to everyone affected. Then, follow up after the fact to make sure it’s still in place.
If it’s not, reevaluate the policy or procedure and decide whether to keep it in your safety program guidelines. It’s okay to change your mind and take something out. Remember, the key to a successful program is continuously improving and perfecting your approach.
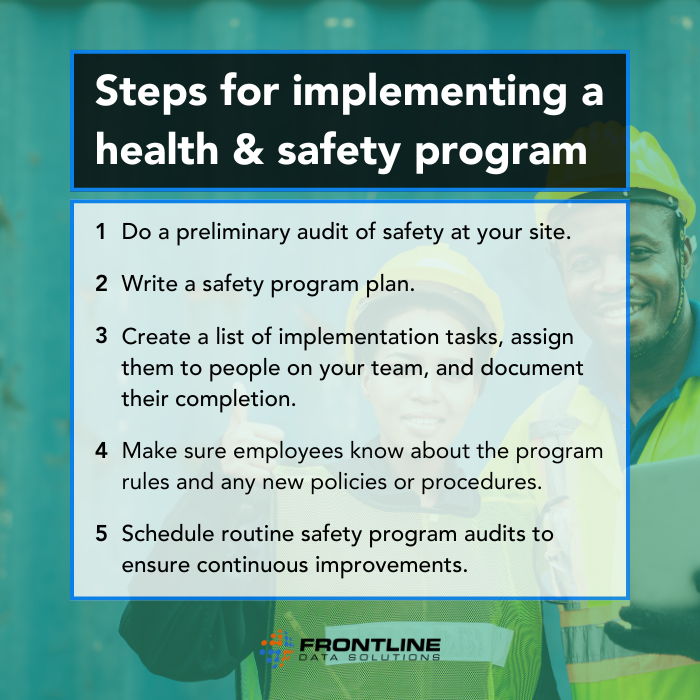
Keep making improvements
After you implement a safety program, the work doesn’t stop. There will always be new ways to improve the procedures and policies you have in place. In fact, getting the program off the ground is just the beginning of a never-ending process.
My best advice would be to schedule periodic audits of different components within your safety program. This includes things like training, documentation, and procedures. Do a full audit at least once per year to keep your safety program up to date and effective.
And don’t forget to get valuable input from your frontline workers during these audits. In EHS management, there’s no better source of information than the people who perform the daily processes you’re trying to make safer. If you stay proactive and receptive to feedback, you should have no problem implementing an effective, long-lasting safety program at your facility.
Other posts you might like…
No posts