We spoke with EHS specialist George Glossop about his experiences managing health and safety risks in industrial environments. Check out the interview below to get his perspective on some of the biggest challenges in everyday life as an EHS professional.
About George Glossop
George Glossop is an EHS Specialist at Amentum, a global engineering and project management solutions provider. He started his career in law enforcement but decided to make a change to EHS after a few years.
While working as an associate for Case New Holland at their IDC facility, he worked directly with the EHS director and discovered a passion for safety. Once a safety training administrator position opened, he jumped at the opportunity and hasn’t looked back since. George has EHS experience in both construction and manufacturing sectors.
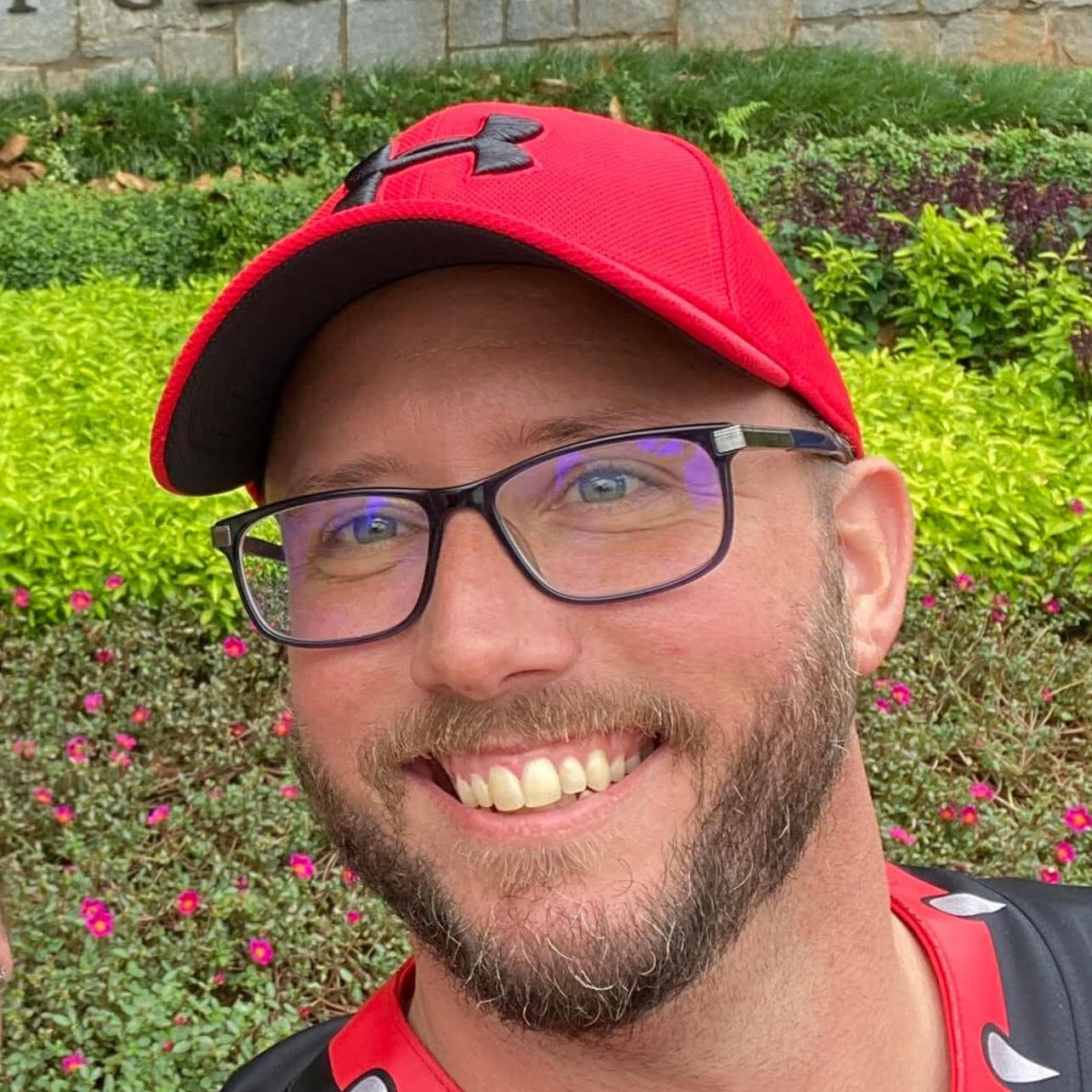
Industrial Safety Management
With a background in both construction and manufacturing, George’s experiences shed light on some of the challenges of managing safety in an industrial setting.
Keep reading to learn more about the ins and outs of everyday safety management, contractor oversight and compliance, and the importance of executive involvement in site EHS performance.
1. As an industrial safety specialist, what are the tasks/activities you spend the most time on in any given week?
As a multi-site manager, what I spend my time on varies a lot because each site is drastically different. At one site, I manage the contractor management program. At my other sites, I deal a lot with our employee training for things like lockout tagout and confined space safety.hnical expertise to design, implement, and validate safety control systems in compliance with these standards.
2. Which safety hazards require most of your time to manage?
Fall hazards and chemical exposures are probably the two hazards that I deal with the most at my sites. At my home site, we have a chem line that requires a yearly clean out. This process alone requires months of planning and coordination with multiple parties.
3. What are the non-negotiable preventative measures your team has in place to control industrial safety hazards?
The number one preventative measure that comes to mind is NO LIVE ELECTRICAL WORK. We also do a lot of confined space entry with elevated platforms at my sites.
For context, our customer builds jet engines. When they drop tools or other pieces in the process, those items sometimes slip through openings in the lifts. For that reason, we have strict rules that you can’t go into the pits until the engine is out of the stand and the platform is empty.
4. What’s the biggest challenge you’ve come across trying to implement a successful industrial safety program?
The biggest hurdle I’ve faced is generational differences. The older generation tends to be stuck in their ways, while the younger ones tend to just do what they want without thought. Bridging those gaps has proven to be a challenge but it has been fun, too. Looking back, it’s made me closer to my teammates and given me a better understanding of where they’re coming from when any issues come up.
5. What role should the safety department play in contractor management? Are there any best practices you can share for making sure everyone on site is qualified and compliant with regulatory requirements?
The safety department should really be the lead in contractor management. Even if, like me, you’re a nested contractor for your company or customer, you should still lead their safety program.
The EHS manager for my customer and I meet daily with the onsite contractor. We have our contractors submit documents like training records, OSHA 300 logs, and insurance certificates before we approve them to come on site.
I’d say our best practice is to walk the site each day (multiple times a day) and meet with the contractors. And we don’t just talk to the foremen. We make sure to get involved with each employee so we can truly know who’s working with us.
6. What role should upper management play in the site’s safety initiatives?
When I was a frontline worker, I appreciated it when an upper-level manager was willing to stand shoulder to shoulder with me on a job. This is one thing I do myself now. I’m willing to be the first person to do a job in a confined space after completing our safety checks.
I truly believe that if the opportunity’s there, upper management should be involved with the work taking place. When executives see what frontline employees deal with, it promotes openness and willingness to collaborate from both parties. This bridges the gap between frontline employees and management.
7. What would be your advice to someone who’s just starting their industrial safety career and maybe feels overwhelmed trying to manage their workload?
ASK FOR HELP. The willingness to ask for help is not a weakness. Help doesn’t have to only come from within your company. With tools like LinkedIn, it’s way too easy to connect with subject matter experts for you not to do it.
Resources, Advice, and Shoutouts
Check out some of George’s recommendations for developing skills and knowledge as a safety specialist!
What’s your favorite resource for staying engaged in EHS?
One of my favorite resources is Drew Hinton, the President of Arrow Safety. He has many years of safety under his belt and experience as a firefighter (like me with my law enforcement work). I’ve attended some of his classes and plan on going to more in the future. I’d recommend following him on LinkedIn.
Is there anyone you want to give a shout out to?
Of course! I want to say how appreciative I am to work with the people I do:
Michael Gimpel, Michael Taylor, Dave Templeton, Lanie Hazelwood, and Jennifer Dearman
You guys are awesome!
George’s Best Advice to Safety Specialists
To put it bluntly: “SHUT UP AND LISTEN AND LEAVE YOUR DESK.” I know there comes a time when we must speak up, but sometimes just listening to concerns before we act is important. Don’t be the safety person that lives at your desk. Get away from it and get involved with the work that is taking place. Try to understand what those frontline employees are dealing with.