As an EHS professional, there’s nothing more painful than hearing that there’s been one or more ergonomic injuries. They’re difficult to deal with because you have to maintain a high level of employee care while working through the care management side of safety at the same time.
The difficulty of managing musculoskeletal injuries
Musculoskeletal injuries pose many challenges for the employee and definitely for us as EHS professionals. An employee may have an injury they don’t know about for minutes, hours, or even more.
I’ve seen many injuries where an employee goes home for the night and doesn’t feel the injury until later in the evening. Usually, they think it’s a small “tweak” and don’t say anything until they can’t sleep at night.
This poses some challenges for quick and effective treatment. After all, the goal of treatment is to correct the injury prior to the onset of long-term issues. This is the outcome of effective case management.
Getting an ergonomic study
When you look at workplace ergonomic injuries, they’re typically the result of poor ergonomic conditions or processes. The best-case scenario is to team with your insurance provider to obtain an ergonomic study at your facility, which includes ergonomic recommendations you may be able to implement.
The downside is that these studies are often expensive, so many companies can’t afford them. But I’d highly recommend this preventative action because it almost always provides valuable insights that your team can use to make improvements.
If you can’t get a study completed through your insurance company for any variety of reasons, you may be able to obtain an ergonomic tool online. You can obtain a generic one from OSHA, here, although you should really dig into ergonomic factors more than just a generic OSHA worksheet.
Performing a site assessment
Performing a full site assessment is crucial in preventing ergonomic injuries. What you won’t get from a generic template is a site-specific understanding of the hazards your workers deal with every day.
That only comes from walking the site and observing the processes and behaviors that may cause these injuries. Here are few things to consider when performing your own site assessment:
- What kind of body positioning do workers use in each process?
- How repetitive are the tasks that workers perform?
- What is the relative height of employee workstations and equipment?
- Do workstations have preventative control measures in place? (Mats, chairs, etc.)
In addition to observing current processes, you should also review past injury data. Look at injuries, first aid incidents, and near misses to find patterns.
For example, is there a specific process or department that produces the majority of incidents? If so, you should consider starting in that area, for the best chance of reducing injury rates.
When addressing the issues you uncover, it’s best to involve other departments and stakeholders (employees, safety committee, upper management, etc.). I would also recommend you involve your engineers if possible.
Get creative with your solutions. Perhaps if you’re trying to prevent workers from lifting heavy objects all day, you can consider hydraulic lift tables/vehicles to take over those tasks. Not every idea you have will work, but it’s important to stay creative and open-minded to unique solutions.
Being proactive in your approach
Because ergonomic injuries can drag on for quite a while, it’s best to eliminate the hazards that cause them as quickly as possible. Even though they’re fairly commonplace (regardless of industry), these types of injuries are not inevitable.
As always, your goal should be to remove the conditions that allow workers to develop unsafe habits. If you can rearrange workstations or redesign processes, you might find relatively cost-effective measures to reduce incident rates at your site.
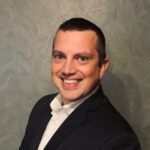
Jason Hathcoat
Jason is a seasoned EHS professional with more than 17 years of experience working in health and safety. He currently works as an EHS manager for a large global HVAC company.
Other posts you might like…
No posts