As an EHS professional, how many times have you gone to a site and either seen or heard something that wasn’t there before? This could be a new piece of equipment, a different process sequence, new materials, chemicals, etc.
It could even be changes to the personnel onsite like a new general manager or an entire department of people.
There are so many companies that have a great process for managing change, while there are probably just as many (or more) who have absolutely no process for this crucial piece of EHS management.
Why is management of change so important?
One of our vital functions in EHS is to mitigate risks. And introducing new changes without carefully reviewing them first can introduce a ton of risks without your knowledge.
You have a responsibility to help identify safety concerns. If you don’t know the risks your workers face every day, it’ll be impossible to control them. When you make changes without a standard process in place, it creates a lot of unintended consequences and rework.
For example, you buy a new piece of process equipment and immediately install it without considering how it affects other variables in the process. Then, you realize that the system now introduces major safety hazards because there aren’t adequate machine guards in place.
So, not only do you have to spend money to retrofit guards, but maybe you also have to shut down the work area and lose production time as well.
Instead of constantly putting out fires caused by organizational changes, implement an MOC process that controls how these changes are rolled out across the site.
Why is MOC so often a missed step in the process?
Unless you’re regulated by OSHA’s PSM standard, which includes MOC requirements, you’re not required to have this sort of program onsite.
Many companies, as I said, just don’t have a change management of system in place. They don’t really have a standard work and don’t any control documents to help guide people through his process.
Within a company, there has to be an inherent desire to manage changes. Because if there isn’t, any system you introduce won’t be followed and therefore won’t last.
You really have to recognize the value of implementing changes carefully before you can begin to set this standard for your team.
EHS is only as good as the top employee of the company wants it to be. If it’s important to that person, or people, then it’ll be done. Bottom line: senior leaders must believe that management of change is a value-added process in order for it to work.
Why should everyone have a change management process?
If you’re trying to argue the case for an MOC process, put it this way:
The issues created by haphazard change implementation cost the company more money than it would cost to invest in an MOC solution.
Those costs come from employee injuries, rework costs, waste disposal, industrial hygiene testing, and any other backend expenses you might incur unexpectedly.
I’ve implemented MOC programs at companies simply by showing senior managers these expenses laid out next to the safety benefits as well. My advice is to take some past projects and get the cost details from them.
Look for areas where a missed step in the process resulted in additional cost—cost that could have been avoided if there’d been a change review before implementation. Present your findings to senior management with the solution of implementing an MOC program.
If there is no MOC process for your company, I strongly urge you to advocate for one. You should have a well-defined process for changes. You will be able to stop fighting so many fires and start progressing your EHS department towards meaningful improvements.
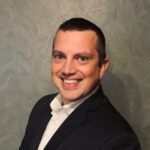
Jason Hathcoat
Jason is a seasoned EHS professional with more than 17 years of experience working in health and safety. He currently works as an EHS manager for a large global HVAC company.
Other posts you might like…
No posts