We connected with Harold Joubert to discuss best practices for oil and gas mechanical inspections. This interview covers the challenges of inspection and maintenance, mechanical integrity, and employee training.
About Harold Joubert
Harold Joubert is the Director of Mechanical Services at Innovative Plant Solutions. He began his career in Non-Destructive Testing (NDT) and Mechanical Integrity (MI) Program implementation shortly after high school. Over the course of his professional journey, Harold received API certifications from the American Petroleum Institute, which gave him the technical expertise necessary to ensure asset reliability and safety.
Over the years, he has worked in management roles within the inspection industry, overseeing complex integrity programs and operations. And because his work has spanned multiple regions, Harold has developed a full understanding and mastery of global industry standards and best practices for oil and gas mechanical inspections.
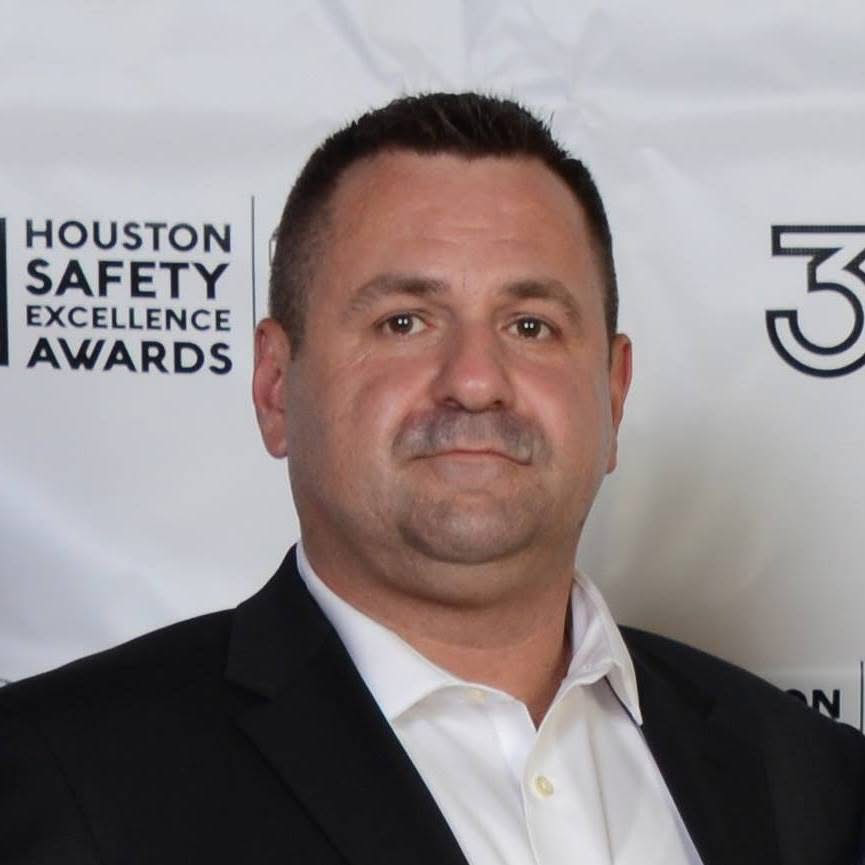
Oil and Gas Mechanical Inspections
Harold has more than 30 years of mechanical integrity and inspection related experience in the petrochemicals industry. In his role, he oversees all aspects of the mechanical integrity services his team provides across industries.
1. Can you walk us through the key steps of a high-quality mechanical inspection? What are the main things you’re looking for?
For a typical mechanical inspection, I follow a systematic process so I can capture the same information each time. The main things I look for during an inspection are the integrity, performance, and safety of the equipment or system.
My process steps are usually planning, execution, and reporting with an emphasis on finding potential welding defects, ensuring compliance with relevant standards, and evaluating potentially damaged mechanisms that could affect the equipment during its operational life.
I actually outlined these steps in this article about preparing for an intrusive inspection for anyone who wants to know more about my process.
2. In your experience, what challenges do companies typically face when it comes to both preventative and corrective mechanical inspection and maintenance?
The main one I see is limited resources, whether that’s people, time, or budget to devote to inspections and maintenance. Another issue I see a lot in oil and gas facilities is the impact of production downtime. If you’re not doing regular maintenance, these shutdowns have a much bigger effect on project completion.
Of course, the more complex your equipment, the more challenges you’re going to face. You really need a solid maintenance schedule to keep up with regulatory changes and deal with aging systems in need of regular repairs. Aside from that, I think it’s important to invest in technology and ongoing staff training to make sure your team’s keeping up with the mechanical integrity of your facility.
3. Can you share a specific example of how you’ve been able to reduce operational costs or solve complex safety issues through the mechanical inspection and repair process?
During a routine external inspection at an oil and gas refinery, my inspectors found early signs of corrosion under insulation (CUI) on several pressure vessels operating at moderate temperatures. Our ultrasonic thickness (UT) readings revealed localized thinning of 20-30%, threatening the vessels’ structural integrity and posing safety and operational risks. This included potential containment loss and unscheduled shutdowns.
To address the issue, we used non-invasive inspection techniques, such as Pulsed Eddy Current (PEC) and Real-Time Radiography (RTR) to detect CUI hotspots without removing large sections of insulation. That way, we only had to remove insulation in affected areas, minimizing labor and material costs. Then, we cleaned damaged areas through abrasive blasting and restored wall thickness using weld build-up and metallic composite wraps for less severe thinning.
To prevent future CUI, we replaced old insulation with closed-cell insulation, added drainage channels and vapor barriers, and applied a CUI-resistant coating before re-insulating. This helped us to decrease inspection and repair costs by 40%, extend the vessels’ lifespan, and improve safety and operational reliability by preventing costly failures and minimizing downtime.
4. What are the training topics related to mechanical integrity that you think all frontline workers should receive?
Nothing compares with hands-on experience and working directly with subject matter experts to get better at oil and gas mechanical inspections. The main training topics related to mechanical integrity that I like to cover are:
- API 510, 570, and 653 for pressure vessel, piping, and tank inspection standards
- API 580 & 581 to learn risk assessment and prioritization of MI activities
- ASME and NACE to focus on material integrity, corrosion control, and FFS assessments
- Inspectioneering Training for industry-specific MI program implementation and NDT techniques
- OSHA 1910.119 for requirements under PSM regulations
I also really like the TÜV Rheinland Academy for mechanical and asset integrity courses and LinkedIn learning for general reliability engineering courses.
In my opinion, frontline workers play a critical role in maintaining mechanical integrity and ensuring equipment reliability, safety, and compliance. There are so many great resources out there to help your team improve their knowledge and skills, so make sure you check these out!
5. You’ve worked across refining, petrochemical, and offshore industries. What are the biggest differences in mechanical inspections between these sectors?
It’s true that mechanical integrity inspections share common principles across industries. From my experience, the environment, equipment, and operational risks create distinct differences in inspection practices between refining, petrochemical, and offshore sectors.
The biggest difference between different types of oil and gas mechanical inspections is what I’m focused on. In the refining process, I’m mainly looking at corrosion risks and asset longevity. With petrochemicals, I definitely prioritize chemical compatibility and pressure integrity. On the other hand, offshore equipment inspections tend to center around structural integrity (given the corrosive marine environment).
6. In your opinion, what’s the best way to balance efficiency with thoroughness when completing inspections in high-risk environments? How do you make sure the work is done right and on schedule?
I’d say the key to this is having a standard approach. Before you do any inspection, you should have a clear list of priorities and risk thresholds. You want to make sure you’re tackling the highest-risk areas first.
Use checklists or inspection software to document everything so you have a solid paper trail for all the work your team’s doing. This is critical for not only compliance but also comes in handy when you’re explaining recommendations to people higher up than you.
I’ve found that time management tools and regular progress assessments are enough to make sure my team stays on track with deadlines. But if you have to delay a project or do secondary inspections, you need to communicate that early so you’re not causing an issue for the operations team.
7. How do you assess the effectiveness of an existing mechanical integrity program, and what metrics do you track?
In mechanical integrity programs, the starting point for measuring success should always be whether you’re compliant with industry standards. For oil and gas companies, this includes things like OSHA’s PSM standard or API certifications.
I’d recommend you look at metrics like MTBF, or “mean time between failures,” to gauge whether your inspection and maintenance activities are working. You could also look at things like equipment-related downtime or repair costs.
From the administrative side, I also like to look at how my team’s performing. Are we completing inspections on time? What kind of backlog do we have for repairs? What’s our response time to tickets? What is the quality of our documentation?
And you can’t forget the impact that oil and gas mechanical inspections have on safety. Always review recent safety incidents and the equipment involved in them. This should guide not only your corrective maintenance tasks, but it should also drive your preventative maintenance program too.
8. For anyone looking to improve the quality of their inspection processes, where would you recommend that they start? What should they focus on first?
I’ve found that if you want to make any sort of improvements to mechanical services, you have to get buy-in from upper management. They need to understand the value of your inspection program, not only from a safety and compliance standpoint but also in terms of long-term operational efficiency and cost savings, for it to be effective. Without management’s full support, securing the necessary funding and resources will be challenging, potentially limiting the program’s effectiveness.
Once management is on board, make sure you communicate these important benefits:
- Reduced downtime
- Minimized equipment failure
- Improved safety performance
- Extended asset life
These all contribute to higher operational reliability and lower maintenance costs. The focus should then shift to defining clear inspection standards, ensuring thorough documentation, and aligning inspection intervals with risk factors to maximize asset integrity. In my experience, a high-quality mechanical inspection program comes at a cost, but the return on investment far exceeds the initial investment.
Harold’s Favorite EHS Resources
We asked Harold to share some of his favorite EHS resources. Check out his recommendations below!
The Inspectioneering Journal
To keep it simple, my personal favorite EHS resource is The Inspectioneering Journal. They have great information for anyone who’s involved or interested in asset mechanical integrity.
Best EHS Advice
“Always be proactive, not reactive. It’s so easy to get caught up in fixing problems after they happen, but the real impact comes from anticipating and preventing issues before they even arise.”