Personal protective equipment — or PPE, for short — is a critical part of any workplace. It helps protect and safeguard workers from potential hazards. OSHA has various standards in place that require workers to follow specific guidelines when using PPE. In this blog, we’ll discuss the different types of PPE, OSHA’s general requirements, and how to determine if you need it.
Types of PPE
Workers wear PPE to protect themselves from potential hazards that can occur in the workplace. Proper use of PPE can increase the quality of your workday. PPE use should be part of every company’s EHS standard operating procedure. Types of PPE include:
Respiratory protection
- Safety glasses
- Goggles
- Face shield
Respiratory protection
- Respirators (for filtering)
- Breathing apparatus
Head protection
- Hard hats (Class G, E, C)
- Bump caps
- Helmets
Ear protection
- Earmuffs
- Ear plugs
- Over-ear headsets
Foot protection
- Metatarsal guards
- Electrically conducted boots
- Water/slip-proof boots
- Safety toe boots
Hand protection
- Impact/puncture-resistant gloves
- Leather gloves
- Latex gloves
- Kevlar gloves
Body protection
- Full body suits
- Welding apron
- Laboratory coat
- Plastic or rubber clothing
- High visibility vests
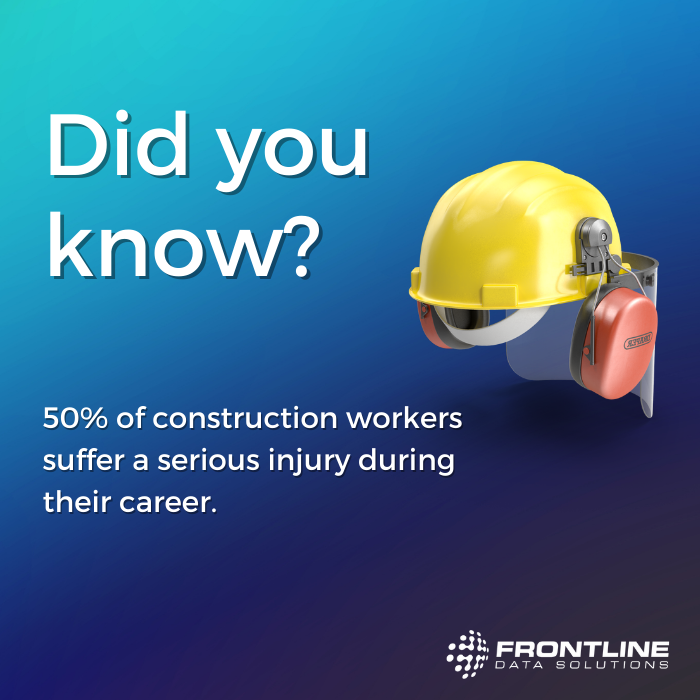
Identifying PPE hazards
To determine whether PPE is necessary, employers must conduct hazard assessments to define the areas where workers are exposed to hazards. This assessment should be repeated before selecting the PPE needed, when the person involved or the task required changes, and when a PPE is not in the condition to be used.
PPE assessment can be conducted with a checklist or through action tracking software. There is also the requirement of training workers on proper PPE use and its documentation. If there are hazards or the potential of hazards, employers need to identify the affected employees and provide properly fitted protective equipment.
Some questions to ask when doing a hazard assessment are:
- Do employees handle, or work near employees who handle hazardous liquid chemicals or encounter blood splashes?
- Do employees work with or near exposed electrical wiring or components?
- Are employees exposed to loud noise from machines, tools, music systems, etc.?
- Do your employees’ hands encounter tools or materials that might scrape, bruise, or cut?
PPE general requirements
Below are some of OSHA’s general PPE requirements that businesses need to consider.
Eye and face protection
Employers are required to provide and ensure the use of PPE for all employees who are at risk of being exposed to eye or face hazards. So, what is an eye or face hazard? If an employee works with flying particles, like light radiation, chemical liquids or gases, or any other potentially dangerous material, they must wear eye protection to protect them from flying debris.
In case of being exposed to light radiation, employees should also use filter lenses with their equipment. Workers with prescription lenses should be provided with equipment that is suitable to use with their lenses. The manufacturer of the protective equipment should be easily distinguishable in case there is any need for contact.
Respiratory protection
Respiratory protection covers the mouth and nose or the entire face to help prevent injuries. Respirators protect workers from the potentially dangerous effects of fumes, vapors, dust, smoke, gas, or other harmful materials that might contaminate breathing air.
If workers must use PRE (protective respiratory equipment), the equipment fit for personal use, comply with NIOSH requirements, and undergo regular maintenance to be effective.
Head protection
OSHA requires employers to make sure their workers are using head protection. Head protection protects workers from falling objects, contact with exposed beams or pipes, or electrical hazards. It’s also a requirement that workers with long hair protect their hair from catching in machine parts.
Foot protection
Protective footwear can help avoid hazards such as rolling or sharp objects, falling, hot surfaces, or electrical hazards. The equipment used in foot protection must comply with ASTM (American Society for Testing and Materials) requirements. This means they have to undergo testing for protective strength, durability, and impact resistance.
Ear protection
Ear protection such as earplugs and earmuffs help prevent hearing loss or impairment. Employers must provide hearing protectors for employees exposed to an average of 85 decibels in an 8-hour timeframe. OSHA recommends self-forming earplugs like foam or waxed cotton to provide a good fit for protection.
Hand protection
Hand injuries include lacerations, fractures, cuts, abrasions, burns, or shocks to the arms, hands, fingers, and fingernails. Workers who are exposed to harmful substances or infectious agents that can damage skin, employees who use tools, equipment, or electrical systems that could result in injuries are required to use hand and arm protection.
Body protection
Exposure to extreme heat or cold, radiation, splashes from hazardous liquids or chemicals, and impact from machinery are all examples that require full-body protection. Fabrics such as fire-resistant wool, nylon, neoprene, or PBI are common materials for making protective equipment for the body.
Required PPE for body protection must be durable against surface contaminations, temperature, the amount of contact and time involved, and the physical state of chemicals.
An important thing to remember when choosing the right personal protective equipment for your job is that it needs to fit you properly, and you need to be able to use it comfortably. A good fit is one of the most important factors in protecting yourself from injury on the job.