In 1971, the US government formed OSHA to better protect American employees at work. OSHA’s primary function was, and still is, to develop, implement, and enforce safety standards for businesses across the country. Today, OSHA recordkeeping regulations affect how businesses report and track events in the workplace. This includes a detailed set of rules for the recordkeeping of injuries, illnesses, and deaths.
History of OSHA compliance
OSHA’s recordkeeping rules apply to certain types of businesses depending on how many employees you have. You can find these rules listed underneath OSHA standard 29 CFR 1904.
One of the things that it states is which types of industries must provide specific documentation. Between the years 1996 and 1998, OSHA used the Standard Industrial Classification (SIC) system and historical safety data from the Bureau of Labor Statistics (BLS).
In 2015, OSHA updated the recordkeeping requirements for more than a million businesses. This change switched over to determining applicable businesses using the North American Industry Classification System (NAICS) and BLS data. Despite the update, businesses with ten or fewer employees are still exempt from having to consistently keep records.
OSHA’s changes also made it so that qualified employers would now have to report amputations, loss of an eye, and inpatient hospitalizations within 24 hours of when they happened. The goal of these changes is to improve the accessibility of data regarding workplace injuries and illnesses. And the regulation also helps businesses find and eliminate potential hazards faster.
The importance of OSHA recordkeeping
Keeping detailed records of workplace injuries and illnesses is beneficial for your business and the industry. Without proper reporting and documentation, OSHA cannot track and analyze incident trends. This makes it more difficult to decide how to address common safety hazards and issues.
Here are some of the other main reasons why recordkeeping is an essential practice:
- Reporting keeps employers focused on safety procedures and outcomes. With better records, safety teams can better find ways to improve and make their facilities safer for workers.
- Injury and illness data allows companies to notice trends and common occurrences. Without this data, safety teams would be operating solely based on assumptions and guesses.
- Safety programs are easier to propose, implement, and manage with concrete injury data.
- OSHA can use data from organizational safety reports to choose which types of events to focus on.
But these benefits only exist if businesses follow the proper recordkeeping requirements. While the required documents aren’t too complicated to fill out, it is sometimes confusing to know when they apply to you.
OSHA recordkeeping criteria
Most businesses must keep routine documentation of workplace injuries and illnesses. But if you have ten or fewer employees, you won’t need to file these documents. Keep in mind that if your workforce grows, OSHA does require you to, regardless of whether you hire one extra employee or twenty.
The employee requirement includes all full-time, part-time, temporary, and seasonal workers within a calendar year. Even if you only hired someone for the holiday rush, you need to make sure to keep these documents in hand.
This workforce size rule also applies to companies who may have their employees separated across different facilities. If you have 6 employees working in a factory and 5 employees working in a warehouse, that is a total of 11 employees, and you’re required to follow OSHA’s recordkeeping rules.
Aside from workforce size exemptions, OSHA also has exemptions for certain types of industries. You can find OSHA’s partially exempt industries here. You will notice that many of the exemptions are for office-based businesses, including companies like:
- Dental and medical offices
- Shoe stores
- Accounting firms
- Colleges and other schools
- Music and TV businesses
For the most part, 24 CF 1904 applies to businesses which pose a high risk for workplace incidents. This includes areas like manufacturing, chemical and gas, oil, construction, etc. Just make sure that you verify where your company stands before disregarding this OSHA requirement. If you’ve determined that you do fall under 24 CF 1904, you need to get the correct recordkeeping forms and make sure you fill them out after each qualified incident.
Submitting forms electronically
As of March 2024, you must submit your OSHA forms electronically through the agency’s Injury Tracking Application (ITA). You can either submit a CSV file, submit using an API, or enter your data manually into the system.
There are only three exemptions from this requirement:
- You had 19 or fewer employees in the past calendar year regardless of what industry you’re in.
- Your company is listed in OSHA’s non-mandatory Appendix A to Subpart B regardless of how many employees you had.
- You had between 20 and 249 employees in the past calendar year and your industry is not listed in Appendix A to Subpart E.
OSHA’s goal in requiring a digital form submission is to make it easier to organize and analyze industry data. Failing to meet this electronic requirement can lead to a citation, so make sure you keep an updated, digital copy of your records at all times.
Filling Out OSHA forms
To remain in compliance with OSHA recordkeeping regulations, there are three main forms you must provide. They are:
- OSHA Form 300: Log of work-related injuries and illnesses
- OSHA Form 300A: Summary of work-related injuries and illnesses
- OSHA Form 301: Injury and illness incident report
Forms 300 and 301 are completed on a continuous basis while form 300A is filed annually. You can use a different type of form to record events, but your forms include all the same data and content as the OSHA-provided forms. You can find them in PDF and Excel formats here.
OSHA defines workplace injuries and illnesses as abnormal conditions or disorders. This definition includes things like:
- Sprains
- Fractures
- Cuts
- Skin diseases
- Respiratory conditions
Note that workplace exposures which do not result in signs or symptoms should not be recorded under this definition.
Another important consideration is how the employee became injured or ill. OSHA does not require businesses to keep a record of all injuries—just the ones that happen during the performance of workplace duties. This includes:
- Cases caused by events or exposures in the work environment
- Cases contributed to by events or exposures in the work environment
If your employee has a preexisting condition that worsens or presents new symptoms as the result of the work environment or duties, it qualifies as an OSHA-recordable event.
Form 300
OSHA Form 300 for work-related injuries and illnesses is relatively straightforward to fill out. Some important things to remember:
- Column “G” is for cases involving a death (needs to be reported to OSHA within 8 hours).
- Column “M” is for marking whether it involved an injury or illness.
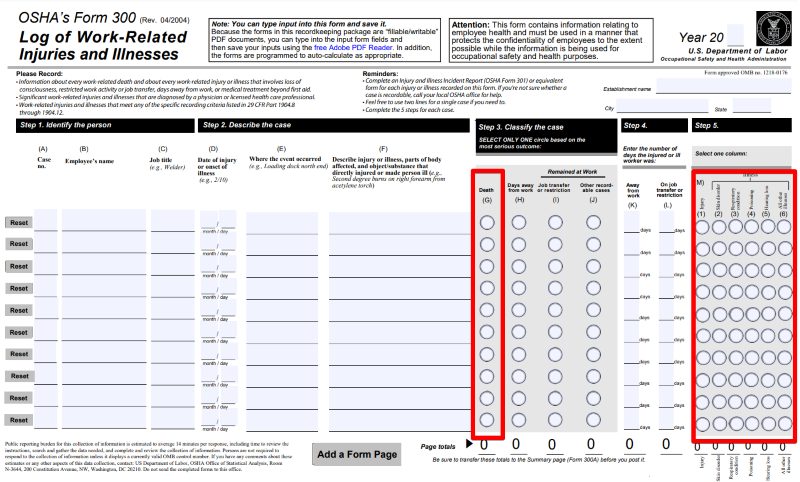
Form 300A
OSHA Form 300A is only filled out once per year. It is a basic summary of how many injuries, deaths, and illnesses you have suffered at your facility. This should be easy to fill out if you’ve kept your other forms organized.
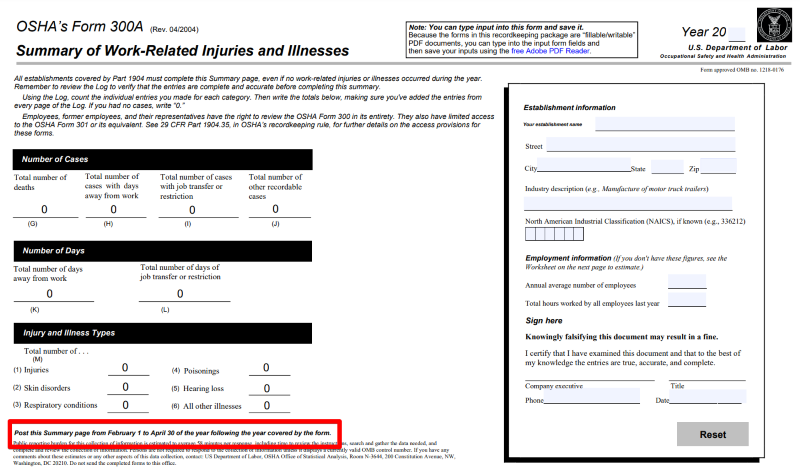
Form 301
OSHA Form 301 must be filled out within seven days of when you become aware of an injury. Make sure that this information is stored safely, as it includes health information for a specific worker.
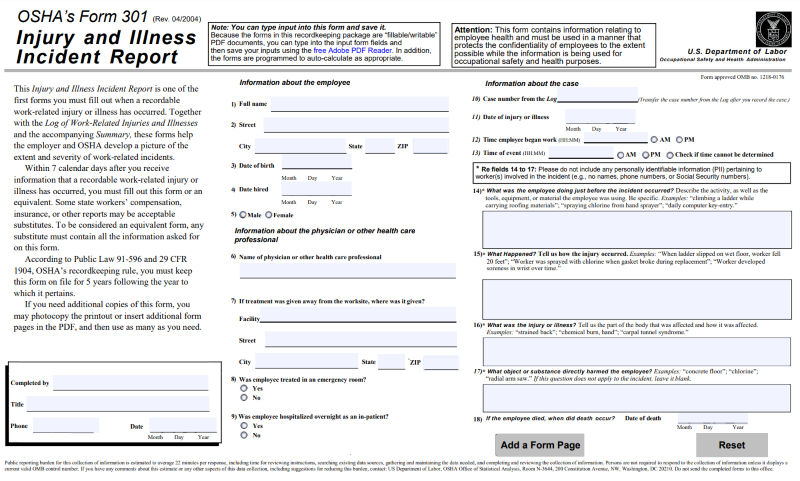
Recordkeeping best practices
The various OSHA injury and illness forms are relatively simple and easy to navigate. The problem that most facilities have is keeping their records organized. Remember, OSHA can request information from you at a moment’s notice.
Whether you’re just starting out or have been in business for a long time, you need a good system for filing reports. If you use paper forms, store them in an easily accessible area. Consider making copies and storing them in a secondary location in case something happens to the original copies.
You can refer to these reports to analyze your own site’s common injuries and illnesses. This should give you an idea of where to make process improvements and safety upgrades throughout your facility.