I remember when some of my high school friends joined the pipeline. It seemed like a great job where you could make a lot of money.
They would come back to our hometown and talk about the excitement of the work, the money, and all the time off they were getting. I’ll admit, I was somewhat jealous of these jobs.
But while it sounded great, none of my friends were the EHS professionals behind the scenes. They weren’t the ones attempting to organize the process (or build it from the ground up, in some cases).
In the past few decades, many companies have made life easier for EHS pros by helping to streamline processes. But there are still many companies that battle with safety issues.
In my experience the top three pipeline safety problems that companies deal with include:
- Having a relatively small, transient workforce
- Conducting effective and efficient training
- Performing routine pre-use equipment inspections
Let’s discuss each of these in more detail, so you can understand where to focus your attention.
Small, transient workforce
The pipeline workforce is a relatively small one. And this is a group of people that tends to have below average hiring practices.
Generally, you have a foreman running a crew. Oftentimes, this person already has pre-selected crews that come with them to nearly every job. Sometimes, the crew members may change. For the most part, however, there aren’t any major switches.
Companies hire the foreman who then brings his/her own crew to the worksite. But there are many issues that come along with this “package deal” situation.
Problem employees
First, problem employees are likely to return to your company even if you’re able to vacate them on one job. This means you’ll have to deal with them all over again (if they come back with that same foreman).
Unskilled pipeline workers
Another issue you may run into is having people who are not “true craftsman” working onsite. What I mean by this is that you tend to get some people who may be machine operators who bring their spouse as “spotters.”
I’ve had to respond to safety incidents from these unskilled workers before. In my opinion, these types of workers shouldn’t be allowed to perform tasks in any capacity until they’ve been verified as competent.
As an EHS professional, you need to tackle the hiring process before you can see improvements in the quality of the workforce. You can start by controlling pre-employment testing (physicals and substances). I’d also recommend that you perform a skills test (beyond just welding skills) to ensure that workers actually know how to operate machinery.
I can’t tell you how many times I’ve done a skills analysis and found that someone was just operating the equipment based on word-of-mouth instructions from one of their buddies. These workers are a huge liability to your company, so it’s important to weed them out before they get to work.
Pipeline safety training issues
In the same vein as workforce issues, lies the headache of training everyone coming in and out of the jobsite. Truth is, hiring untrained, unskilled workers to operate heavy machinery exposes companies to a whole lot of risk. But that doesn’t mean it’s an uncommon practice in the oil and gas industry.
I’ve seen many “operators” cause injuries or property damage to the pipe or machines because they haven’t received proper training. They lack the skill and knowledge to do the task safely, so they expose the business to major risk.
And here’s a common sentiment that drives insufficient training practices:
Why invest so heavily in training for workers who are just going to leave in a few months to the next opportunity?
This is a terrible struggle for EHS pros in the field who spend their time tracking down workers for training requirements, only to realize those employees are gone. Before long, there’s another batch of employees to train.
But if you’re working for one of these companies, you should never stop trying to implement a solid training program. This is a constant fight within the industry because of the short window between hiring workers and starting a project.
You might be thinking: “What about operator qualifications? Don’t those take care of this problem?”
To that, I’ll say that some companies and trainers do it the right way while others don’t. And it’s not unique to the pipeline—this discrepancy exists in all industries.
It all comes down to your philosophy as an EHS professional. Are you going to fall into the status quo because it’s easier? Or are you going to keep training the right way, regardless of how long it takes you to make a significant impact?
If you’re guided by your principles, then it won’t matter to you whether workers are gone in a few months’ time. At the very least, you’re making the entire industry safer by ensuring that workers receive the proper pipeline safety training to avoid incidents.
Pre-use equipment inspections
I recently talked to one of my good friends (who has been working the pipeline for several years now) about the struggles in different industries.
He told me that the lack of pre-use equipment inspections is one of the biggest root causes of pipeline safety incidents.
Pipeline machinery (excavators, side-booms, bulldozers, etc.) requires operators to perform pre-use inspections. When operators don’t do this, however, they don’t catch faulty or damaged equipment.
This of course, increases the likelihood of incidents happening. And the inspections are designed to eliminate this type of risk altogether.
Most companies probably don’t have enough full-time EHS professionals to complete routine inspections. It’s just not something that leaders tend to view as an investment.
At minimum, however, there should be some accountability from leadership to ensure that these are completed every time. If you’re an EHS specialist or manager who works in an understaffed department, it may be on you to ask for assistance and to not stop until you get it.
EHS software for oil and gas pipelines
You might not need or be able to increase your department’s headcount. But every company should consider process improvements that simplify the burden of managing complex regulatory requirements.
Here are a few of the ways our EHS software solutions can help you tackle the pipeline safety issues outlined in this post:
Contractor Safety Management (CSM): Verify that all contract workers have received their required training.
Learning Management System (LMS): Create, assign, and track training tasks for all of your employees.
Management of Change (MOC): Ensure OSHA PSM compliance by coordinating changes to processes, personnel, and equipment.
Action Tracking (ACT): Assign, log, and review corrective actions, project tasks, and more.
If you’d like to learn more about how these solutions may apply to your business, you can schedule a demo with our sales team.
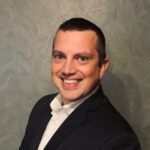
Jason Hathcoat
Jason is a seasoned EHS professional with more than 17 years of experience working in health and safety. He currently works as an EHS manager for a large global HVAC company.