When we think of EHS reporting, the first thing that comes to mind is reporting employee workplace injuries. But the reporting process actually goes much deeper than that.
Let’s take a moment to consider Heinrich’s accident pyramid.
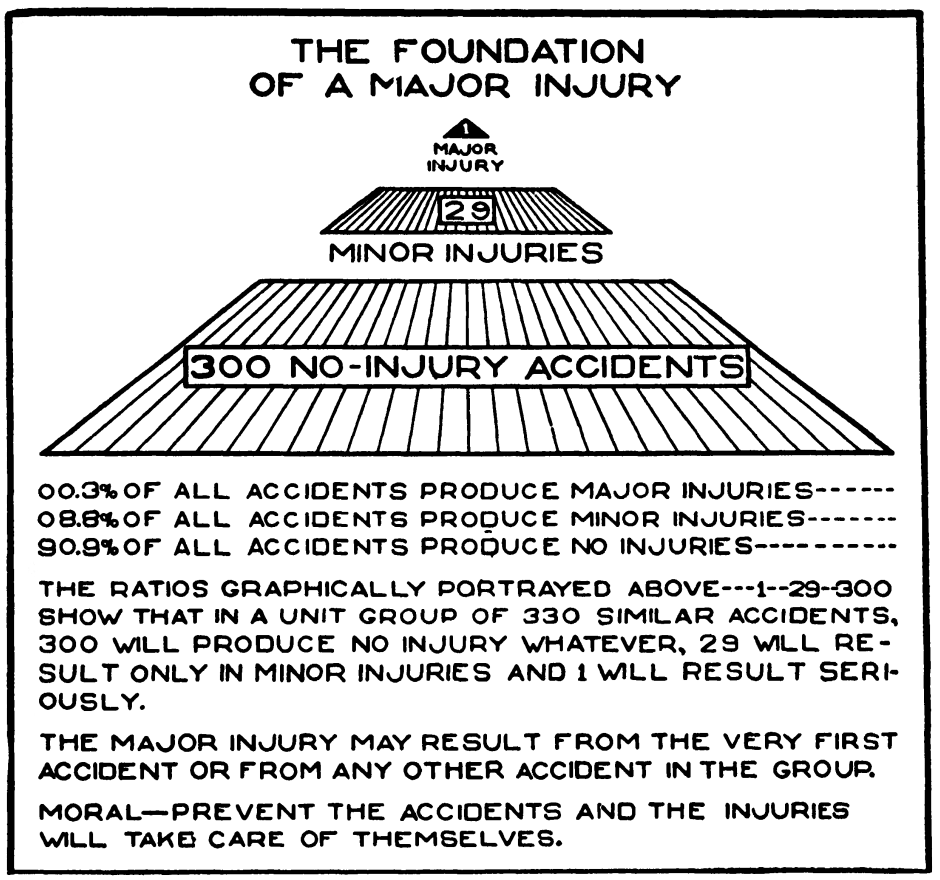
When you group together 330 similar incidents, you’ll have about 300 that never cause an injury (equal to roughly 90%). Another 29 of those 330 will be minor incidents, and only 1 of those incidents will result in a major injury.
[You can learn more about this concept here]
While this doesn’t play out exactly the same way for each operation, we must acknowledge the fact that we’ll deal with several near misses and minor injuries until we experience a major incident.
From my experience, I can tell you I have rarely seen a company reporting 329 incidents prior to the major injury. In fact, those numbers rarely come close.
At my current employer, the team was reporting less than 10 first aid incidents annually. With just under 1.5 million exposure hours, I knew that number was significantly lower than reality.
And so, I set out to tackle this discrepancy to see if we could increase the number of reported incidents. There were five main steps in my approach:
- Review the current process and reporting documents.
- Collect employee and supervisor feedback.
- Make necessary revisions to documents and processes.
- Announce and execute changes.
- Revisit with additional feedback and/or changes.
Below, I’ll tell you how I went about restructuring our reporting process to make it more efficient and more valuable at preventing incidents.
Review the current reporting process
The first step in the restructuring process is to look at how your team currently reports incidents and injuries.
When I first got to my current employer, there was a lengthy process just to report an employee getting a band aid for a minor finger laceration. The team filled out a long report, and management rarely knew about these incidents because there was such a lag.
The report itself was difficult to navigate and confusing to fill out. Not to mention, the behavior-based safety (BBS) observations were several pages long.
I determined that the current process was too complex and time-consuming. This, in part, made a major contribution to the severe underreporting of safety incidents.
Collect employee and supervisor feedback
The next thing I did was to speak with employees about the reporting process. They all told me the process was difficult and took too much time to complete. The paperwork was cumbersome, and it was just easier to get the first aid supplies without any of the other “hassle.”
Supervisors told me they had difficulty navigating the current incident report. They also said that the observation reports were way too long and usually resulted in little to no information gathered anyway. Additionally, with observations, they didn’t want any repercussions from putting their name on them.
Another roadblock for the employees was the lack of distribution of the reporting documents. In other words, even if they wanted to report something, they couldn’t locate the form or submit it anonymously if needed.
This was a critical step in understanding exactly what changes I needed to make.
Revise your process and documents
My first thought was to make reporting much easier and less cumbersome.
First, the form had to go. I needed to make it shorter, easier to fill out, and more convenient to access. To do this, I changed the initial employee report form for observations, first aid incidents, and near misses. I also included an “other” section for miscellaneous use cases.
Then, I made the form into a small 3×4” card with information on the front and back. I added several drop boxes throughout the facility, along with holders to stock the cards. Once a card was turned in, HSE staff would be able to review it immediately and determine whether to file a follow-up report.
I also changed the incident report, improving the flow of the information. This helped to make it easier to navigate for both the people filling it out and the people reading it.
Announce and execute changes
After all the changes were made, I needed to let everyone know. Here are a couple of ways I did it (and you can too):
- Explain the new process at toolbox talks.
- Put it on communication screens/boards.
- Send emails to affected groups/parties.
- Advertise it in the HSE newsletter.
During this communication step, you really need to explain the anonymity of reporting observations. Obviously, reporting injuries is different. However, you want employees to feel comfortable reporting things to you, knowing that you won’t divulge their identity (if possible). Once you get that trust from people, you should see some increase in observations.
Revisit and evaluate the process
After you fully restructure your EHS reporting process, you may see significant improvements. However, you should constantly be evaluating the effectiveness of your systems and processes.
Inevitably, over time, you’ll start to see some decrease in reporting compared to prior years. This is the time to visit with employees and supervision to figure out the reason.
Essentially, you should go back to the employee and supervisor feedback step of this approach. Underlying issues, such as management changes or employee turnover, could be the cause of your reporting process decline. If this is the case, you should be able to reset your expectations and ensure compliance.
Just by looking at your current process, listening to employees/supervisors, and making some small changes, you have the potential to really improve your site’s EHS reporting process.
I believe following this approach will help you find incident trends and identify major areas of improvement. In my experience, it should help you make changes that positively impact your site’s safety performance.
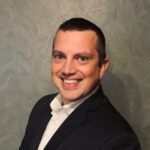
Jason Hathcoat
Jason is a seasoned EHS professional with more than 17 years of experience working in health and safety. He currently works as an EHS manager for a large global HVAC company.