We spoke to Marlyn Gitomer, CSP, about the ins and outs of safety committee leadership for EHS professionals. From this interview, you’ll learn about the challenges of running an effective committee and what you can do to improve the outcomes of your meetings.
About Marlyn Gitomer
Marlyn Gitomer is the Founder and Principal Consultant of Safety Beta LLC, an occupational health & safety consulting firm with 14 years of experience in the EHS field.
Like many of her peers, she got into EHS by accident. While on a demolition project collecting evidence for a litigation case, she had a near miss that could have been a serious injury. When reporting the incident to her employer, Marlyn discovered two things:
- Near misses could happen to her
- She wanted to help protect workers from similar situations
Shortly after this experience, Marlyn started working as a health and safety coordinator and began learning safety on the job. Since those early days, she has worked in private and public sectors for both construction and general industries.
She has clients in a variety of industries, including manufacturing, hospitality, education, food and beverage, aviation, pharmaceutical R&D, and waste management (to name a few).
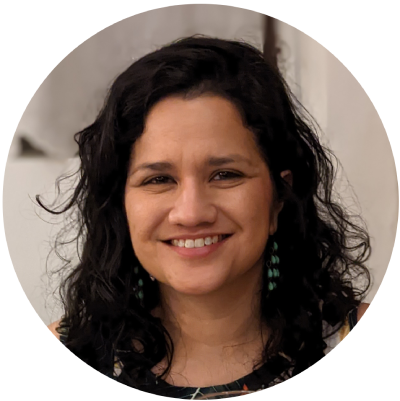
Safety Committee Leadership
Marlyn has about 8 years of experience with safety committee leadership. Since gaining experience in her early years as an EHS coordinator, she’s led safety committees for both a municipality and a client in telecommunications.
1. What are the main challenges that come with managing a safety committee and making sure it stays active and purposeful?
Trust. As a leader, you have to earn the trust and confidence of your safety committee members. They need to believe that you are competent and knowledgeable, and they need to know that you have their best interests in mind. Be open to their ideas and be willing to listen. Never make it about blame. Celebrate positive behaviors whenever possible.
2. In your experience, why do safety committees fail? What makes them successful in the long term?
Like any other business initiative, safety committees fail when there’s no clear purpose, when senior leadership does not offer support, or when there’s a lack of trust between employees and management. Good communication and accountability are two major factors in the long-term success of a safety committee.
3. What are some signs that a site might need a safety committee?
Safety committee requirements vary from state to state. OSHA published a white paper in April 2016 titled “Safety and Health Programs in the States” which provides a great reference. I’d recommend looking at Table 1 for an overview of applicability.
My best advice would be to check regularly for regulation changes. Even if your state doesn’t require you to have a safety committee, it’s a good idea to implement one if:
- You’re experiencing high or increasing incident rates.
- You have high-hazard or high-risk operations.
- Your company is growing or expanding into new functions that might increase risk.
4. What resources or processes do you think should already be in place before starting a safety committee? What are the essentials?
A safety committee should have full support from senior leadership. This includes commitment to real change, investment of resources like time, money, and people, and accountability from the top to the bottom of the organization.
Management should play the role of liaison and focus on communication between senior leadership and the front line. Some employees may be unengaged or unwilling to sit on a committee—try not to force them to participate. Instead, find your safety champions and give them an opportunity to lead by example. Once everyone is on board to form a committee, set clear goals and create a strategy for success. Revisit those goals often and adjust them as needed.
5. Where do you think safety committees can have the biggest impact on the site? Should they focus on identifying issues versus fixing them?
Every site is different, but you can’t fix what you don’t know is broken.
Safety committees should employ hazard identification and risk assessments before recommending corrective action plans. They should also conduct periodic audits and inspections to ensure their programs work. And, above all, the committee should have a strong communication plan with employees to include educational materials and training appropriate for each job level and type.
I don’t think it’s necessarily the job of the safety committee to fix things directly, but I do think it’s their job to ensure that there’s accountability for the people responsible for those fixes.
6. What’s your advice for anyone who either wants to create or gets put in charge of a safety committee but isn’t quite sure where to start?
Two things:
- Talk to other leaders in your industry who run safety committees and learn from their challenges, mistakes, and successes.
- Ask yourself (or your boss) “Why are we starting a safety committee?” Make sure that you have a clear purpose before you start assembling a team.
Marlyn’s Professional Resources Recommendations
We asked Marlyn to share the main resources she uses to stay updated on EHS best practices. Check out her recommendations below!
EHS Leadership Resources
Monthly magazines like ASSP’s Professional Safety and AIHA’s The Synergist are great to keep tabs on emerging topics. As a member of both organizations, I attend several conferences each year and enjoy learning from my peers from all across the nation.
Recently, I’ve been exploring tools such as chat boxes and Safety Champion to learn how I can better serve my clients through the use of AI and technology. It’s an exciting time to be in EHS!
Advice for EHS Professionals
“You won’t always have the answers. Know when to ask for help from others.”