Starting at a new company as an EHS manager
Starting at a new company in the EHS field can be extremely challenging. My colleagues frequently tell me they have no clue where to begin with the EHS program at a new site.
Hiring managers oftentimes don’t know enough about EHS to properly update us on the status of the program, any ongoing projects, or really much of anything. It’s a situation I’ve been in before:
You come in on your first day and someone from HR helps you get settled into your office with your equipment. Then, they say: “I’m right down the hall if you need anything!” But once you’re all alone, you’re left to immediately begin making decisions about a site you know relatively nothing about.
Everyone has their own path forward in this situation, but I want to share the strategies that have helped me through it. Hopefully, you can learn from my experiences to power through those difficult first few weeks at your new company.
Assess the current state of affairs
When starting at a new company, even if you have a good transition into the role, you need to know where the program currently stands. Start on the frontlines to see the processes your company has in place.
You can’t really know how effective the EHS program is if you don’t know what’s really going on. And you can only do that by spending substantial time with the employees and their supervisors.
Here are some questions you should start by answering:
- What are the major processes within the operation?
- Do workers practice safe behaviors?
- How do supervisors approach safety?
- Are both workers and supervisors aware of the site’s safety protocols?
The goal during this initial assessment is to find gaps in the EHS program that you can address once you get started. This is a balanced process—you don’t want to come in and immediately start telling people what they’re doing wrong. Your role at this point is only to identify areas of improvement.
I’ve seen some EHS professionals really rub employers the wrong way on day one. Remember, it’s not just what you say but how you say it. Before making recommendations, be sure that you fully understand the operation.
Manage your time wisely to perform an effective gap analysis. I’d recommend scheduling some time on your calendar for program review. Then, take that time to review current policies, procedures, and standard work, as well as other programs in place.
I’d strongly urge you to audit your company in the eyes of an external auditor. This will give you a good indication of where you need to spend your time. The major difference is that you’ll also be the one coming up with creative, workable solutions.
Build strong relationships with workers
The first few weeks are crucial for building strong relationships with the workforce in your facility. This is especially true of the frontline workers whose trust you need to create a solid EHS program.
You’ll get so much more information from workers and supervisors once they trust you to tell you all the details (good and bad). You simply can’t succeed in EHS today without these connections.
Figure out what workers like about the EHS program and what pains them. I’ve personally never had an issue building relationships with workers while in the EHS department. The best advice I can give you is to be willing to listen and take notes when possible. This shows that not only are you listening but that you plan to use the insights as well.
Devise a plan of action
Once you find gaps in the EHS program, plan out how you’re going to close them. Give yourself reasonable but ambitious target dates to finish.
Remember, when starting at a new company, you’ll have responsibilities consistently trickling in for the first few months. As you settle in your role, others will expect more from you. So, if you can course correct in the first few weeks, you’ll be in good shape for long-term success.
Ask for help where you need it from others in the company. Don’t be shy—remember your role is to improve and optimize the EHS program. Show senior leaders that you’re resourceful and proactive by using all the tools already available.
I’ll tell you this: every single company has pain points within its EHS department. If you dedicate yourself to finding, understanding, and tackling these issues right away, you’ll be much more likely to build a solid EHS program that you’ll be proud to run.
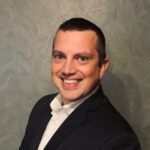
Jason Hathcoat
Jason is a seasoned EHS professional with more than 17 years of experience working in health and safety. He currently works as an EHS manager for a large global HVAC company.