Many factors determine a company’s long-term success. Quality, not just of goods and services, but the processes that create them as well, is necessary to achieve higher levels of performance. And adopting the principles of total quality management (TQM) is a great way to do just that.
What is total quality management?
Total quality management, or “TQM” for short, is a framework for achieving company-wide quality in many areas of performance. The idea behind TQM is that you can greatly improve your products and services by improving your internal processes and procedures.
It revolves around the participation of all employees in quality management practices. This framework requires you to standardize quality control measures while also allowing for flexibility in the application of TQM techniques and principles.
How does TQM improve quality?
Variables like work processes, employee behaviors, training, and procedures affect the quality of your outputs. TQM improves quality by optimizing these inputs so they’re as effective as possible. In other words, the better your internal processes, the better products and services you’ll produce.
What are the benefits of TQM?
The main difference between quality management and total quality management is the scope of the approach. While QM addresses product and service quality, TQM addresses quality throughout the company, covering both process outputs and inputs.
Due to this holistic approach, TQM benefits an organization by:
- Improving customer service, satisfaction, and loyalty
- Producing higher quality products and services
- Making internal processes more efficient
- Increasing productivity
- Reducing operational costs and process waste/rework
- Boosting employee engagement
- Creating greater brand recognition and perception
- Allowing for better decision making
Of course, you can only reap these benefits if you follow the TQM framework properly. This means creating systems and policies that align with the principles of total quality management. But it also means committing to continued oversight, so that you can continue to improve upon your strategy.
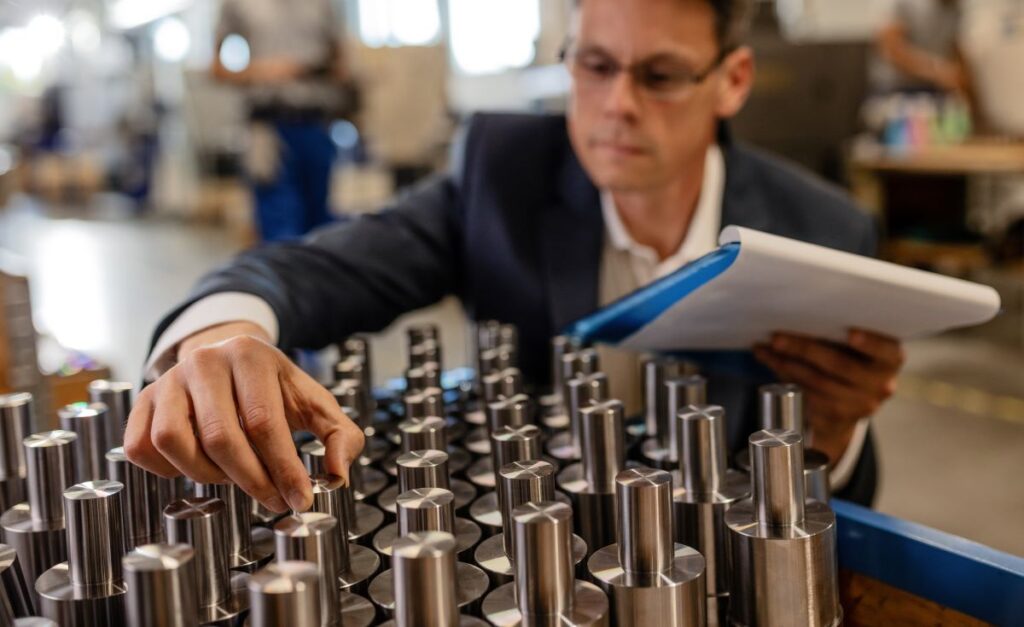
What does TQM involve?
The main guiding principes of total quality management include:
- A focus on the customer experience
- Continuous improvement of process inputs and outputs
- Employee involvement in the system
- Data-driven decisions
- Full TQM integration across all systems
- Methodical approach to implementation of the QM strategy
A well-rounded TQM strategy considers the impact of operational decisions on three main stakeholders: your customers, your employees, and your processes and systems.
Customers
The focus of TQM (and any quality management system) is customer experience. Providing excellent products, services, and customer support is the only way to ensure your brand’s longevity.
TQM takes a normal quality management approach farther by addressing other areas of customer satisfaction. For example, what is the quality of the sales discovery or onboarding process? How well do you treat existing clients? Considering these aspects of customer experience is vital to success.
Employees
Employee involvement is one of the main drivers of TQM. After all, your employees are closest to the customers and process inputs that determine quality. Teaching your workers about quality management and allowing them to collaborate on quality initiatives helps foster a proactive approach.
Another tenet of TQM is data-based decision making. Employees play an important role in collecting and analyzing the information and metrics you’ll need to make operational decisions that improve quality. Gather insights from your team on the areas of performance they think are worth improving and investing in. Worker input is a great way to find continuous improvement project ideas.
Processes and systems
Unlike regular QM strategies, a total quality approach also tackles the quality of internal processes and systems. The idea is that by optimizing internal processes, you’ll also produce better outputs for employees and customers.
You can apply TQM principles to all sorts of systems, including:
- Employee onboarding, training, retention, and experience
- Environmental, health, and safety compliance
- Logistics and materials procurement
- Loss prevention
- Quality assurance
- IT and data management
The goal is to continuously improve process inputs so outputs can improve as well. To do this, you need to treat them as interconnected and consider how any changes will affect all areas of the operation—not just customers.
How is TQM implemented?
Because total quality management isn’t a regulatory requirement, there’s no rulebook for how to implement it. This can make it hard to get started, but it also allows for more creativity. In the long run, having a site-specific quality management strategy is better than adopting a generic approach.
Steps to implementation
While each company has different needs, here are some basic steps for implementing a TQM strategy:
Internal assessment: Review your current quality management strategy and make note of which processes, procedures, equipment, etc., are essential to the customer experience. Use the assessment to identify which areas of your QM strategy need improvement or which ones you need to remove or replace entirely.
Scope and goals: Determine the scope you want your QM strategy to focus on and which goals you want to set as a team or organization.
Plan outline: Create a detailed plan of which QM procedures you want to implement or change. Make sure your plan includes the owner, objectives, timeline, and expected outcome for each step you’re going to take.
Strategy implementation: Start implementing the TQM plan, making sure to verify the correct application of each new procedure, policy, process, etc. Document the implementation process with action tracking software to ensure constant oversight.
TQM integration: Oversee the integration of your TQM strategy across all teams and departments. Provide training to managers and workers on the purpose of any changes or new process inputs you’ve implemented. This step also includes standardizing data collection, documentation, compliance verification, and any other processes related to the site’s TQM plan.
Strategy refinement: Over time, use the data you collect on your quality initiatives to refine your strategy. Form a TQM committee or team to oversee the continuous improvement of your plan and to identify and fix any issues.
For most companies, implementing a TQM strategy takes months and refining it takes years. It’s not something you can “set and forget” either. A commitment to quality means a commitment to continuous improvement and iteration. But if you stay open-minded to feedback from both customers and employees, then you should have no problem fully embracing the principles of total quality management and using them to your advantage.