We spoke with Subena Colligan about what it really takes to transform EHS performance and find solutions that work. Her answers shine a light on the need for adaptive and prescriptive programs that tackle systemic flaws, not just surface level issues.
About Subena Colligan
Subena Colligan is the CEO of EHS Transformation Consultants. She has 16 years of experience in health and safety, and today she’s a prominent voice in the EHS community.
Years ago, Subena recognized that many talented EHS professionals don’t get to run the safety programs they’re capable of building because they’re constantly responding to and correcting issues. She started EHS Transformation Consultants to enhance resources for EHS departments that want more effective and sustainable EHS programs. Her firm provides temporary staffing and expertise to audit EHS systems, create corrective strategies, and implement solutions to close the gaps.
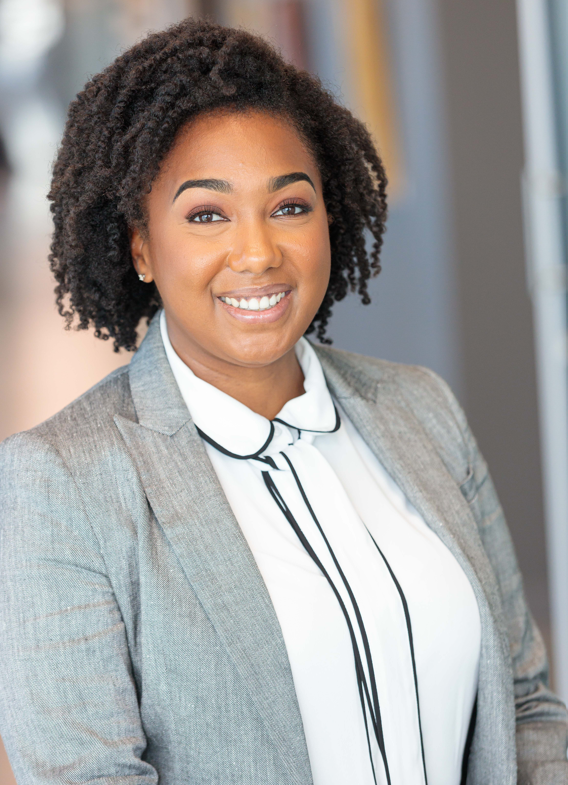
EHS Solutions That Work
Subena got her start in EHS as an Industrial Hygienist for the United States Air Force. Since then, she has worked in several industries, including government, aerospace, consumer goods manufacturing, higher education, and food manufacturing.
1. Why do so many companies struggle to go beyond regulatory compliance?
Compliance is not a “one size fits all” situation. Some companies accept the risk of regulatory noncompliance for various reasons. Most often, I find that the business outcome (profit, meeting metrics, etc.) outweighs the benefit of meeting regulatory requirements.
Some companies just don’t have the subject matter expertise to meet or exceed requirements. More than 90% of all US manufacturers have 20 employees or less. An operation like that may not have the capacity for a full-time EHS manager to move the business beyond regulatory compliance.
Of course, large companies that employee thousands of workers have to develop systems that meet the needs of many different operations.
But regardless of the situation, meeting regulatory requirements is just the starting point, the bare minimum. It’s ironic to me that so many organizations expect their talent to go beyond the status quo, driving business growth and innovation. Yet, when it comes to workplace wellbeing, they do just enough to check the box, rather than truly investing in their employees’ needs.
2. What are the main arguments against investing in more effective EHS solutions?
There are plenty of arguments, especially around regulation. But companies that don’t invest in EHS solutions that work, in my opinion, don’t want more profit.
Seriously, in the US there’s a strong correlation between EHS performance and increased financial performance. I read about a company with high EHS performance that saw a 7% increase in its market cap and a 12% revenue increase in the past decade.
Whatever someone’s argument is, the data and business outcomes can’t deny that companies with high EHS performance have a greater return on investment.
3. In your experience, what are the major signs that a company or facility is ready to take its EHS program to the next level?
The executive leadership is investing in transformation and/or growth or wants to be market leaders. These executives know that you’re only as capable as your weakest link. They’re aware of the value that upskilling their workforce delivers. These are the leaders who take a holistic look at every system contributing to their company’s success and prioritize long-term results over short-term gains.
4. For anyone who wants to transform their EHS program, where would you advise them to start?
At EHS Transformation Consultants, we use a framework that allows us to be consistent in every organization. The first question we ask is, what do you want to achieve and why? We ask this question to both EHS and operations leaders. That’s because transformation takes 18-36 months to achieve and the EHS department can’t do it all alone. Your “why” needs to go beyond a “flavor of the month” program change. This allows us to use the resources we deploy effectively without being wasteful.
5. When you first audit an EHS program, what do you look for? What are some common issues you typically find?
Typically, the main things we look for are management and leadership engagement, training effectiveness, employee participation, contractor safety management, hazard management, and regulatory compliance conformance. These areas give us a view of the different levers that are pushing and pulling your EHS program.
The most common issue I encounter is gaps in the roles, responsibilities, authorities, and accountabilities of management regarding the EHS program. As a result, the EHS department often ends up driving the program instead of all levels of the organization actively engaging.
In my experience, evaluating process changes is one of the best ways to determine how well the organization functions. For example, if you introduce a new piece of equipment and neither the EHS team nor the general manager knows about it, this highlights a breakdown in communication and reveals opportunities to strengthen the management system across the organization.
6. Do you often see a discrepancy between what clients say needs to be fixed and what you find to be the issues? If so, why do you think that is?
While we uncover underlying concerns, the issues causing immediate pain are always valid. However, they’re often symptoms of a deeper root cause.
For example, one of my manufacturing clients was experiencing amputations on different lines at multiple locations, all involving the same type of equipment. Leadership initially attributed the incidents to poor decision-making, believing operators were failing to use “common sense” when reaching into the equipment. From the perspective of maintenance professionals—who had extensive training in hazardous energy control—it seemed obvious that reaching into the equipment was a dangerous choice.
However, our investigation revealed a critical gap: maintenance personnel weren’t exposed to the same hazard because they only worked on the equipment when it was properly shut down, ensuring hazardous energy was controlled. Operators, on the other hand, faced these issues in real time, under the pressure of production cycles and perceived time constraints. Their actions were not simply poor decisions, they were driven by an environment that did not account for the realities of their work.
Furthermore, when one site implemented an engineered safeguard to mitigate the risk, there was no communication to ensure the same control was applied at other locations with the identical hazard. Most concerning was the presence of a blame culture, where the focus was on individual actions rather than systemic failures. True accountability required upper management to take decisive action—pausing operations until an effective control was implemented and holding the right stakeholders responsible for eliminating the risk of severe injury.
7. For anyone who wants to transform their EHS program, where would you advise them to start?
A well-resourced strategic plan with clear tactical actions will always be my go-to approach. This provides the framework for what you’ll say “yes” to, ensuring that your decisions align with your overarching goals.
Often, the challenge isn’t just about saying “yes” but about the difficulty of saying “no.” Without a clear strategy, you risk spreading your limited expertise too thin.
With a well-defined plan, every decision reaffirms your strategy. Sometimes, this means turning down projects or initiatives that divert focus—but even those refusals are a “yes” to executing the plan effectively and staying on course for long-term success.
8. How have your clients at EHS Transformation Consultants found success using your recommendations for solutions that work?
Supporting the EHS profession is a wonderful way to share our team’s talent with the world. Most importantly, receiving positive client feedback is the greatest satisfaction. One comment that stuck with me and pushed me to keep going was that one of our clients found new methods to reduce significant injuries and fatalities using our solutions. Their executive officer invested $1.2M in the EHS department to further mitigate risk.
At EHS Transformation Consultants, we drive positive business outcomes through our proven transformation model. This includes our three-step approach: Audit. Strategize. Resolve.
Through this process, we deliver tangible, sustainable success for EHS programs. We do this by:
- Identifying gaps
- Developing strategic solutions
- Implementing practical fixes
It’s our mission to help businesses build stronger, more resilient EHS programs that support long-term growth.
Subena’s Favorite Resources
We asked Subena to share some of her favorite EHS resources. Check them out below!
EHS professional resources
I love my professional organizations! American Society of Safety Professionals (ASSP), American Industrial Hygiene Association (AIHA) and National Safety Council (NSC) are all nonprofits that compile the latest in the field. I also like to subscribe to platforms that are innovating in a niche like technology, artificial intelligence, and regulatory updates.
Advice for EHS professionals
“The best professional advice I received was that you are never too experienced to be curious!”