Trip hazards are one of the most common—yet preventable—safety risks in any work environment. While they may not seem as serious as other workplace dangers, trip hazards account for many injuries and lost productivity each year. Addressing them isn’t just a compliance issue, it’s a matter of keeping your team safe and your operations running.
Definition of Trip Hazard
A trip hazard is a physical obstruction or irregularity in a walking surface that can cause a person to stumble or lose their balance. By OSHA’s definition, “any change in floor level that is ¼ inch or more constitutes a tripping hazard.”
Look for these issues during your Gemba walks or safety inspections. Oftentimes, all it takes is a simple fix to remove the hazard entirely and prevent trip injuries.
Trip Injuries
According to the Bureau of Labor Statistics (BLS), there were 39,410 recorded trips in 2023 not involving a fall but still causing employees to miss work. These nonfatal injuries cost companies millions annually in healthcare, lost time, and lowered productivity.
What makes trip hazards especially tricky is that they often blend into the background. If a facility has been operating for a while, employees may stop noticing these dangers altogether. That’s why regular audits and strong housekeeping practices are essential.
Common Trip Hazards
Trip hazards are often easy to spot—but just as easy to overlook. Many come from everyday items or behaviors that have become part of the routine. Here are some of the most common types of trip hazards found in facilities:
- Loose cords and cables
- Unmanaged clutter
- Missing handrails
- Unsecured floor mats, tiles, or carpeting
- Poor lighting
- Uneven walkways
- Open cabinets and doors
- Incorrectly laced shoes or boots
Often, the root cause of these hazards is not poor cleaning practices, but rather operational behavior. A misplaced broom or frequently tripped-over rug isn’t just a mess—it’s a sign of a systemic issue that needs addressing.
Best Practices to Eliminate Trip Hazards
Preventing trip hazards in the workplace starts with a proactive, team-based approach to safety. Here are several strategies that you can use to reduce incidents.
Track and Log Action Items
If the same trip hazard keeps popping up, it’s time to revisit your solution. Repeated issues (like a rug that always bunches up or a broom left in the walkway) may indicate that your current setup isn’t working. Change it—and log what you tried. Consistently documenting hazards and corrective actions shows due diligence and builds a track record of continuous improvement.
Action Tracking with Frontline ACT
Frontline ACT makes it easy to see the status of all your team’s in progress action items!
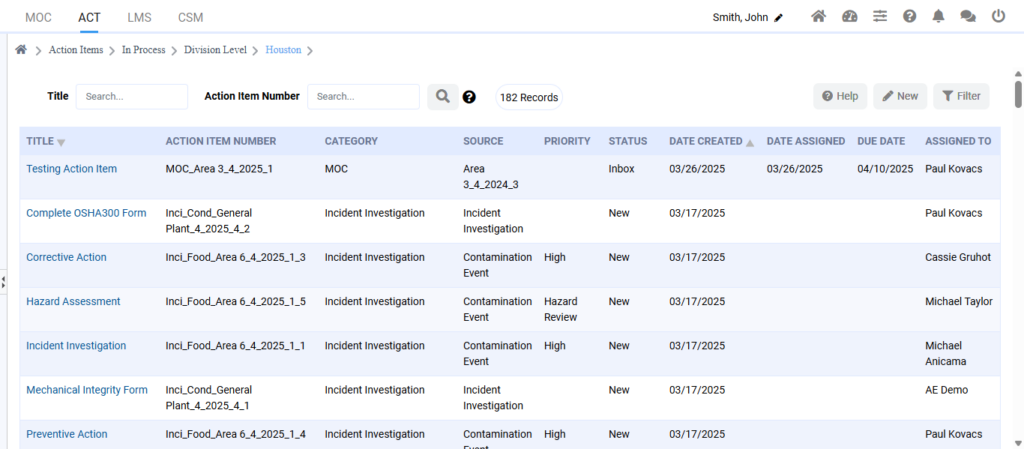
Clean Regularly and Thoroughly
A clean facility is a safer facility. Establish and enforce a regular cleaning schedule that answers these questions:
- Which areas need cleaning?
- How often should they be cleaned?
- Who is responsible for cleaning them?
Audit your cleaning routine often to ensure workers complete tasks and hazards don’t accumulate.
Address Unsafe Behaviors
A major part of facility safety is individual behavior. Workers must practice personal safety to protect not only themselves, but others as well, from injury.
As an operational leader, you can change the culture by addressing these unsafe behaviors immediately when you see them. Log safety observations to find recurring habits that you want your team to break. The key is not to shame workers for bad habits. This may have an adverse effect on morale and ultimately make your team more resistant to safety guidance. Instead, take the time to understand why they’re doing something unsafely, so you can better address the root cause.
Sometimes, you’ll find that bad habits are the result of poor systems, faulty equipment, or unclear procedures. Use these moments as an opportunity to improve your administrative controls.
Reorganize High-Risk Areas
It’s not always possible to fully remove trip hazards. For example, you may need to run a cord across a work area to set up equipment. In this case, you should control the cord with tape to make it less of a trip hazard and more of a “speed bump.”
Use the principles of 5S to organize and improve the layout of your highest-risk work areas. Note which areas are prone to collect clutter. Is there a better way to store the clutter? Consider adding a pallet drop zone, organizational bins, or storage racks to keep the area clear.
Whether you manage a warehouse, manufacturing floor, or office space, recognizing and addressing trip hazards is a key part of workplace safety. From enforcing cleanliness and auditing behaviors to proactively managing recurring issues, there are many ways to prevent injuries and maintain a productive environment.it, come up with a new action item. Doing this allows you to keep a detailed log of all your solutions. That way, if a recordable trip injury occurs, you have a demonstrated history of trying to address the issue.